Advanced Air Purification and Emission Control: The Future of Industrial Filtration
INDUSTRIAL SUPPLIES
2/8/20253 min read
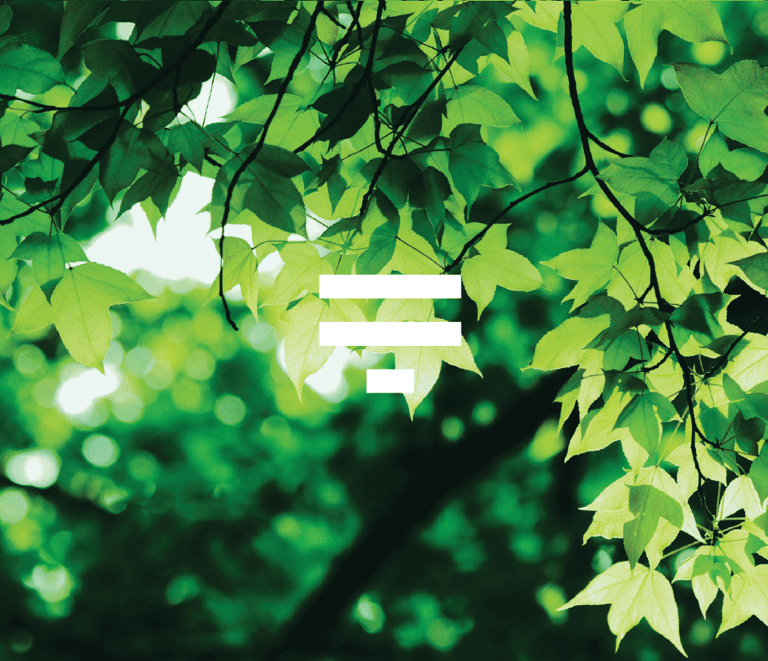
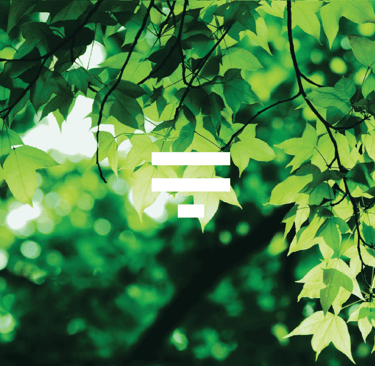
In an era where environmental consciousness is more than just a trend, industries across the globe are striving to minimize their emissions and improve air quality. Advanced filtration technologies have emerged as critical solutions in achieving these goals. From electrostatic precipitators to fabric filters, and from desulfurization to denitrification, each method plays a crucial role in controlling industrial pollutants. This article explores the cutting-edge technologies that industries use to purify emissions, improve operational efficiency, and comply with stringent environmental regulations.
Electrostatic Precipitators: The Power of Static Charge
Electrostatic precipitators (ESP) have long been a cornerstone in industrial air pollution control. These devices leverage the power of electrostatic forces to remove fine particles from exhaust gases.
How Electrostatic Precipitators Work
The polluted air enters the ESP chamber.
High-voltage electrodes ionize the gas, charging dust particles.
Oppositely charged collection plates attract and capture the particles.
The clean air exits while the dust accumulates on the plates and is periodically removed.
Advantages of Electrostatic Precipitators
High Efficiency: ESPs can remove up to 99% of particulate matter.
Low Operating Costs: Compared to other filtration systems, ESPs require less energy for large-scale operations.
Durability: These systems can function effectively over long periods with minimal maintenance.
Industries That Rely on ESPs
Power plants
Cement production facilities
Steel manufacturing units
Pulp and paper mills
Fabric Filters: The Gold Standard in Particulate Capture
Fabric filters, commonly known as baghouse filters, offer one of the most effective methods of capturing fine particulate matter from industrial emissions.
How Fabric Filters Work
Polluted gas is directed through a series of fabric bags.
The fabric acts as a sieve, trapping dust while allowing clean air to pass through.
Periodic cleaning mechanisms remove the accumulated dust from the filter bags.
Key Benefits of Fabric Filters
Superior Filtration Efficiency: Captures up to 99.9% of particulate emissions.
Versatility: Works well in a range of industrial applications, from metalworking to chemical manufacturing.
Compliance with Stringent Regulations: Meets even the most rigorous environmental standards.
Challenges in Baghouse Filtration
Frequent Maintenance: Regular filter replacement is necessary to maintain efficiency.
High-Pressure Drops: Increased airflow resistance can lead to energy-intensive operations.
Desulfurization: Combating Sulfur Emissions for a Cleaner Future
Sulfur dioxide (SO₂) emissions are a major contributor to acid rain and respiratory illnesses. Desulfurization technologies play a crucial role in mitigating these harmful effects.
Popular Desulfurization Methods
Wet Scrubbing: Uses alkaline solutions like limestone or lime to absorb SO₂.
Dry Scrubbing: Involves spraying dry sorbents into the gas stream.
Flue Gas Desulfurization (FGD): The most commonly used process in coal-fired power plants.
Benefits of SO₂ Removal
Reduced Environmental Impact: Prevents acid rain formation and air pollution.
Improved Workplace Safety: Lowers exposure risks for industrial workers.
Recyclable Byproducts: Gypsum, a byproduct of FGD, is valuable in the construction industry.
Industries That Use Desulfurization
Power generation plants
Petroleum refineries
Metal smelting operations
Denitrification: Eliminating Harmful Nitrogen Oxides
Nitrogen oxides (NOx) are potent pollutants that contribute to smog, acid rain, and respiratory issues. Advanced denitrification technologies help reduce these emissions significantly.
Common Denitrification Technologies
Selective Catalytic Reduction (SCR): Converts NOx into harmless nitrogen and water vapor using catalysts like vanadium and titanium dioxide.
Selective Non-Catalytic Reduction (SNCR): Uses ammonia or urea injections to achieve NOx reduction at high temperatures.
Advantages of Denitrification
Significant Emission Reductions: SCR can reduce NOx emissions by up to 95%.
Energy Efficiency: Modern NOx removal systems operate with minimal energy consumption.
Regulatory Compliance: Ensures adherence to strict air quality standards.
Major Industries Utilizing NOx Control
Cement plants
Glass manufacturing
Pulp and paper industries
Other Industrial Filtration and Emission Control Equipment
Beyond ESPs, fabric filters, desulfurization, and denitrification, several additional filtration technologies are essential for comprehensive air quality management.
Cyclone Separators
Uses centrifugal forces to separate particles from gases.
Effective for pre-filtration before more advanced systems.
Wet Scrubbers
Employ liquid absorption to capture pollutants.
Ideal for industries dealing with gaseous pollutants.
Activated Carbon Filters
Excellent for removing volatile organic compounds (VOCs) and odors.
Frequently used in chemical manufacturing and food processing.
Metal Structures: The Backbone of Filtration Systems
Industrial filtration systems depend on robust metal structures to support and house components. These structures must withstand harsh operating conditions, including extreme temperatures and corrosive environments.
Key Materials Used in Filtration System Construction
Stainless Steel: Offers excellent corrosion resistance.
Carbon Steel: Provides high strength at a lower cost.
Aluminum: Lightweight yet durable for specialized applications.
Role of Metal Structures in Industrial Filtration
Provides housing for filter components.
Ensures system durability and stability.
Supports large-scale air purification processes.
Conclusion: The Future of Industrial Filtration
As industries face increasing pressure to curb emissions and enhance sustainability, the evolution of air purification technologies remains vital. From electrostatic precipitators and fabric filters to advanced desulfurization and denitrification processes, the solutions available today are more sophisticated and effective than ever before.
With the integration of cutting-edge filtration systems and durable metal structures, industries can not only meet stringent environmental regulations but also improve efficiency and operational safety. As technology continues to advance, the future of industrial air purification looks promising, paving the way for cleaner, greener industrial processes worldwide.