Exploring Advanced Hose and Pipe Technologies for Modern Industrial Applications
INDUSTRIAL SUPPLIES
5/16/20244 min read
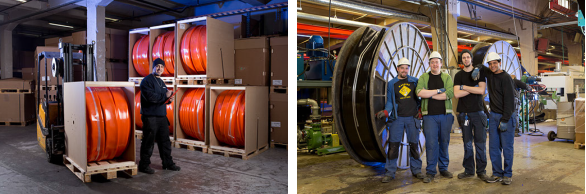
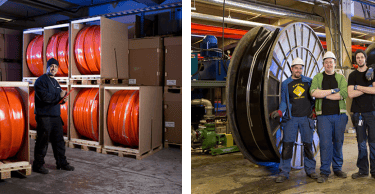
In today's rapidly evolving industrial landscape, the need for robust, efficient, and versatile piping solutions has never been greater. From high-pressure environments to deepwater applications, the technology behind hoses and pipes continues to advance, providing industries with the tools they need to operate effectively and safely. This blog will delve into several key innovations in hose and pipe technology, focusing on high-pressure hoses, U-shape insertion hoses, crimping machines, inversion lining hoses, deepwater flexible pipes, end fittings, steel-cord/wire reinforced flexible pipes, spoolable reinforced composite pipes, and lay-flat hoses.
High-Pressure Hoses: The Backbone of Industrial Operations
High-pressure hoses are essential in many industrial operations, from hydraulic systems to chemical processing plants. These hoses are designed to withstand extreme pressures and harsh conditions, ensuring that they can perform reliably under stress. The materials used in high-pressure hoses, such as reinforced synthetic rubber, thermoplastics, and metal, provide excellent durability and resistance to abrasion, chemicals, and heat.
Key Features of High-Pressure Hoses
Durability: Made from robust materials that can withstand high pressures and harsh environmental conditions.
Flexibility: Despite their strength, these hoses are designed to be flexible, allowing for ease of use in various applications.
Safety: High-pressure hoses are built to prevent leaks and ruptures, ensuring safe operation in critical applications.
U-Shape Insertion Hoses: Innovative Design for Specialized Applications
U-shape insertion hoses are designed for specific applications where traditional straight hoses might not be practical. These hoses are particularly useful in confined spaces or in systems that require a curved hose path. The U-shape design allows for a more compact installation while maintaining the integrity and performance of the hose.
Advantages of U-Shape Insertion Hoses
Space Efficiency: Ideal for use in tight spaces where straight hoses cannot fit.
Enhanced Flow: The smooth curvature helps maintain optimal flow rates and reduces the risk of blockages.
Versatility: Can be used in a variety of applications, from automotive to industrial machinery.
Crimping Machines: Ensuring Secure and Reliable Hose Connections
Crimping machines are essential tools for creating secure connections between hoses and fittings. These machines use hydraulic pressure to compress a metal sleeve around the hose and fitting, ensuring a tight and durable seal. Crimping is crucial in high-pressure applications where secure connections are vital for safety and efficiency.
Benefits of Using Crimping Machines
Precision: Provides consistent and accurate crimps, ensuring reliable connections every time.
Efficiency: Speeds up the assembly process, saving time and labor costs.
Safety: Reduces the risk of leaks and failures, enhancing the overall safety of the system.
Inversion Lining Hoses: Revolutionizing Pipe Rehabilitation
Inversion lining hoses are used in trenchless pipe rehabilitation, a method that allows for the repair of existing pipelines without the need for extensive excavation. This technology involves inserting a flexible liner into the damaged pipe, which is then inverted and cured in place to create a new, seamless pipe within the old one.
Key Benefits of Inversion Lining Hoses
Minimal Disruption: Reduces the need for excavation, minimizing disruption to the surrounding environment and infrastructure.
Cost-Effective: Lower labor and material costs compared to traditional pipe replacement methods.
Durability: Creates a seamless, corrosion-resistant new pipe within the existing one, extending the lifespan of the infrastructure.
Deepwater Flexible Pipes: Meeting the Challenges of Offshore Exploration
Deepwater flexible pipes are designed for use in offshore oil and gas exploration, where they must withstand the extreme pressures and harsh conditions of deepwater environments. These pipes are constructed from multiple layers of materials, including high-strength steel and thermoplastics, to provide the necessary flexibility and durability.
Features of Deepwater Flexible Pipes
High Strength: Built to withstand extreme pressures and the corrosive effects of seawater.
Flexibility: Allows for movement and bending, accommodating the dynamic conditions of offshore operations.
Longevity: Engineered for long-term use, reducing the need for frequent replacements.
End Fittings: The Essential Connectors
End fittings are crucial components in hose and pipe systems, providing the connections needed to attach hoses to equipment, valves, and other hoses. These fittings must be compatible with the hose material and designed to withstand the pressures and conditions of the application.
Importance of Quality End Fittings
Compatibility: Ensures a secure and leak-free connection between hoses and equipment.
Durability: Made from materials that can withstand the same conditions as the hoses they connect.
Versatility: Available in various sizes and configurations to suit different applications.
Steel-Cord/Wire Reinforced Flexible Pipes: Combining Strength and Flexibility
Steel-cord/wire reinforced flexible pipes are designed to provide the strength of steel with the flexibility of a hose. These pipes are used in applications where high pressure and mechanical stress are present, such as in hydraulic systems and heavy machinery.
Advantages of Steel-Cord/Wire Reinforced Pipes
Strength: The steel reinforcement provides exceptional tensile strength and resistance to deformation.
Flexibility: The flexible design allows for easy installation and maneuverability.
Reliability: High resistance to pressure and external impacts, ensuring reliable performance.
Spoolable Reinforced Composite Pipes: Lightweight and Durable Solutions
Spoolable reinforced composite pipes are an innovative solution for transporting fluids and gases. These pipes are made from composite materials, including thermoplastics and fibers, providing a lightweight yet durable alternative to traditional metal pipes.
Benefits of Spoolable Reinforced Composite Pipes
Lightweight: Easier to transport and install compared to metal pipes.
Corrosion-Resistant: Resistant to chemical and environmental corrosion, extending the lifespan of the pipe.
Flexibility: Can be spooled and unspooled easily, making them ideal for long-distance transport applications.
Lay-Flat Hoses: Convenient and Efficient Fluid Transport
Lay-flat hoses are designed for efficient fluid transport and storage. These hoses can be easily rolled up and stored when not in use, making them a practical choice for applications where space and portability are important.
Features of Lay-Flat Hoses
Portability: Easy to transport and store due to their flexible and collapsible design.
Durability: Made from tough materials that can withstand heavy use and harsh conditions.
Versatility: Suitable for a wide range of applications, including irrigation, firefighting, and industrial fluid transport.
Conclusion
The advancements in hose and pipe technology are driving significant improvements in industrial efficiency, safety, and performance. From high-pressure hoses and U-shape insertion hoses to deepwater flexible pipes and spoolable reinforced composite pipes, these innovations are meeting the diverse needs of modern industries. By understanding the unique benefits and applications of each type of hose and pipe, businesses can make informed decisions and select the best solutions for their specific requirements.
As technology continues to evolve, we can expect to see even more sophisticated and specialized hose and pipe solutions emerging, further enhancing the capabilities of industries worldwide. Whether it's through increased durability, flexibility, or ease of installation, these advancements will undoubtedly play a crucial role in shaping the future of industrial operations.