Introduction: Understanding the Growing Demand for IV Bags and Machines
PHARMACEUTICAL MACHINERY
2/1/20257 min read
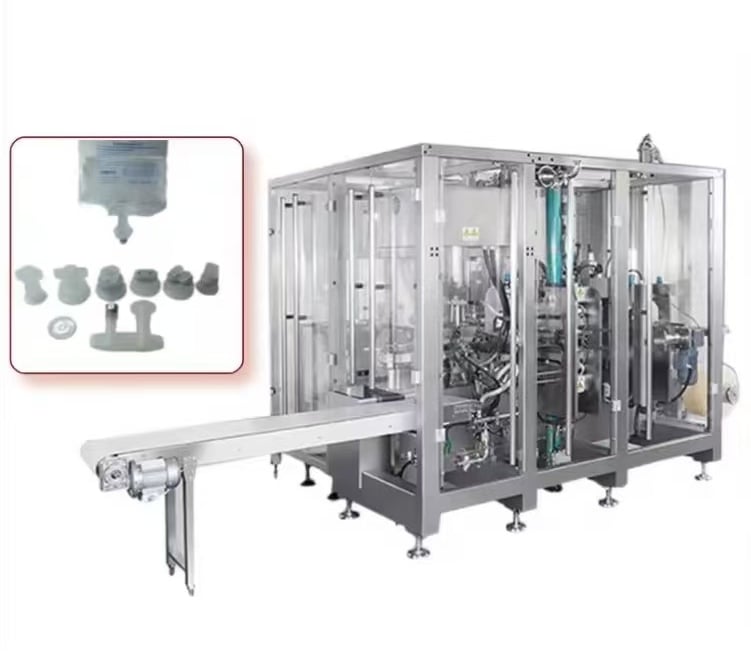
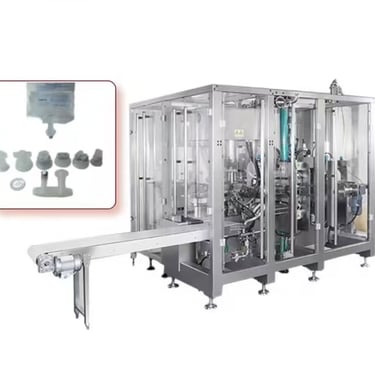
Introduction: Understanding the Growing Demand for IV Bags and Machines
In the healthcare and pharmaceutical industries, intravenous (IV) solutions are fundamental to the delivery of life-saving treatments. These fluids, carefully infused into the bloodstream, are used for a wide range of purposes, including hydration, medication administration, and electrolyte balance restoration. IV bags are crucial in ensuring that these fluids are delivered safely and effectively to patients.
With the ever-increasing demand for medical treatments globally, the need for IV bags and infusion solutions has risen exponentially. From IV infusion sets to plastic bottle LVP production lines, medical professionals rely on these bags for crucial treatments. As healthcare systems scale up to meet the needs of an aging population and address growing healthcare demands, the role of automated manufacturing technologies has never been more important.
The shift toward automation in IV bag production is driven by several factors, including the necessity for higher production volumes, consistency, and improved quality control. Today’s market is flooded with high-tech machines that help manufacturers meet stringent quality standards while maintaining high output rates. Whether it's an automatic IV bag filling machine, an IV bag sealing machine, or a PP bottle IVF infusion solution production line, these innovations help streamline production while ensuring the safety and reliability of every bag produced.
Key Components of an IV Bag Manufacturing Line
The production of IV bags is a complex process that involves a series of machines working together to create a finished product. The goal is to ensure that the bags are produced efficiently, meet all quality standards, and are filled with the appropriate medical solutions in a sterile environment.
1. The IV Bag Production Process
At the heart of IV bag manufacturing is the formation of the bags themselves. Machines like the semi-rigid plastic IV mixing bag forming machine are used to create the bag’s structure. These machines use advanced molding technology to shape the plastic into a flexible bag that can hold large volumes of fluid.
Once the bags are formed, they are moved to the filling stations. The IV solution production line is typically equipped with specialized machines that ensure the correct type and amount of solution is used for each bag. Depending on the machine, the solution may include saline, antibiotics, or other medications necessary for patient treatment.
2. Filling Machines
Filling machines are critical in the IV bag production line. They are responsible for precisely measuring and filling each bag with the required solution. Different types of filling machines are available depending on the viscosity and nature of the solution being filled. For viscous fluids, machines must be capable of handling thicker substances without clogging or causing irregular fills. Conversely, weight liquid filling machines and volumetric liquid filling machines provide precise control over the fluid amounts, ensuring each bag is filled to the exact specification.
There are also machines that cater to specific requirements, such as the BFS IV fluid PP bottle production line for producing IV bags that contain saline or other essential fluids. This line automates the entire process, including bag formation, filling, and sealing, providing a fully integrated solution for large-scale production.
3. Sealing Machines
Once the IV bags are filled, they must be sealed tightly to preserve sterility and prevent contamination during transportation and storage. IV bag sealing machines are responsible for this step. Depending on the type of bag material, these machines use heat, pressure, or a combination of both to form a secure seal. The sealing process is crucial for maintaining the integrity of the bag and the fluid it contains.
Some sealing machines are designed for specific applications. For example, non-PVC soft bag filling and sealing machines are used for producing environmentally friendly and safer options. Non-PVC materials are often preferred in healthcare due to their reduced toxicity and lower environmental impact compared to traditional PVC bags.
4. Labeling and Inspection Machines
The final step in the production line involves labeling and inspection. IV bag labeling machines ensure that every bag is correctly marked with essential information such as the type of fluid, batch number, expiration date, and manufacturer details. The labeling process is essential for traceability and ensuring the correct administration of fluids to patients.
After labeling, bags undergo thorough inspections with IV bag inspection machines to check for defects such as leaks, incorrect sealing, or mislabeling. These machines use sensors and cameras to detect any potential issues, ensuring that only perfect bags move forward in the distribution process.
Types of IV Bags and Their Uses in Healthcare
There are several types of IV bags used in medical treatments, each designed for different applications and types of fluid. The two most common types are IV infusion bags and IV solution bags. Both are essential for delivering intravenous fluids to patients but serve different purposes depending on the medical need.
1. IV Infusion Bags
IV infusion bags are typically used to administer fluids such as saline, electrolytes, or medications. These bags are often made of flexible materials like PVC or non-PVC plastic to allow for easy administration of fluids directly into the bloodstream. Infusion bags are used in a variety of settings, from hospitals and clinics to emergency response situations.
2. IV Solution Bags
IV solution bags, on the other hand, are primarily designed to hold solutions for intravenous therapy, such as nutrient solutions or medications. These bags are often part of a more complex treatment regimen, such as chemotherapy or parenteral nutrition. The design of these bags must ensure that the contents remain sterile and stable for long periods.
Healthcare professionals select the type of bag based on the solution required and the patient’s specific needs. In many cases, non-PVC bags are becoming more popular due to their safety and environmental benefits. Non-PVC materials reduce the risks of toxic leaching and are more easily recyclable than traditional plastic bags.
3. Special Considerations for IV Bags
In addition to material considerations, the design of IV bags can vary depending on the volume of fluid required and the intended duration of treatment. For example, large volume parenteral (LVP) bags are used for continuous fluid administration over extended periods. These are typically made from plastic and are often seen in the IV solution production line for plastic bottle LVP.
Some applications also require more specialized bags, such as IV mini-bags, which are used for small doses of medication. These bags require different machinery, such as IV mini-bag processing machines, to handle the smaller sizes and maintain sterile conditions.
Innovative Machines in IV Bag Production
The rise of automation and specialized machinery has transformed IV bag production. From high-speed automatic filling machines to advanced sealing machines, technology has made it possible to meet the growing demand for IV bags without sacrificing quality. Let’s explore some of the cutting-edge machines currently shaping the industry.
1. Automatic IV Bag Filling Machines
One of the most significant advancements in IV bag production is the automatic IV bag filling machine. These machines are capable of filling thousands of bags per hour, greatly increasing production efficiency. They also reduce the risk of human error, ensuring that the correct amount of solution is added to each bag.
The machines use precise volumetric measurement systems to guarantee that each bag is filled with the correct amount of fluid. Some models also incorporate multiple filling nozzles, allowing for the simultaneous filling of multiple bags, further enhancing throughput.
2. IV Bag Overwrap and Sealing Machines
In addition to filling, IV bag overwrap machines are used to add an additional layer of protection around the filled bags. This overwrap prevents contamination and preserves the sterility of the IV bags, especially during transportation and storage. Once the bags are overwrapped, they move to the IV bag sealing machine, where they are tightly sealed to ensure that no leaks occur during use.
3. Glass and Plastic Bottle IV Solution Production Lines
For manufacturers specializing in glass bottle IV solutions, the glass bottle IV solution production line is an essential piece of equipment. These lines use specialized machines to handle the unique properties of glass, including filling, sealing, and labeling. IV solution production lines for plastic bottle LVP also perform similar tasks but are designed to handle the flexibility and lightweight nature of plastic.
These advanced machines enable manufacturers to switch between glass and plastic bottles quickly, depending on customer needs, all while maintaining high production speeds.
Automation in IV Bag Manufacturing: Advantages and Challenges
Automation has revolutionized the IV bag manufacturing process. However, it comes with both advantages and challenges.
Advantages:
Increased Efficiency: Automation significantly speeds up production, allowing manufacturers to meet high demand without compromising quality.
Improved Accuracy: Automated systems eliminate human error, ensuring that each bag is filled, sealed, and labeled with precision.
Cost Savings: Though the initial investment in automated machinery may be high, over time, the reduction in labor costs and increase in production capacity can lead to significant savings.
Challenges:
Initial Investment: High-tech machines, especially those used in IV solution production lines, can be costly. However, the return on investment over time is substantial.
Technical Skills: Operating advanced machines requires skilled workers who can manage and troubleshoot automated systems. Training and workforce development are essential to ensuring the systems work optimally.
Maintenance: While automated systems require less manual labor, they do require ongoing maintenance to keep the machines running smoothly.
Conclusion: The Evolution of IV Bag Production and the Role of Technology
In conclusion, the IV bag manufacturing industry has undergone significant advancements in recent years. Automated machines, such as IV bag filling machines, sealing machines, and IV solution production lines, have revolutionized production processes, allowing manufacturers to meet increasing demand while ensuring high-quality products.
As the demand for IV bags continues to grow, technological innovations will play a pivotal role in meeting these needs. From advanced non-PVC soft bag filling and sealing machines to high-speed filling machines, the future of IV bag production is clearly focused on efficiency, precision, and sustainability.
By embracing these cutting-edge technologies, manufacturers can ensure that they are well-positioned to deliver safe, reliable, and cost-effective IV bags to healthcare providers around the world.
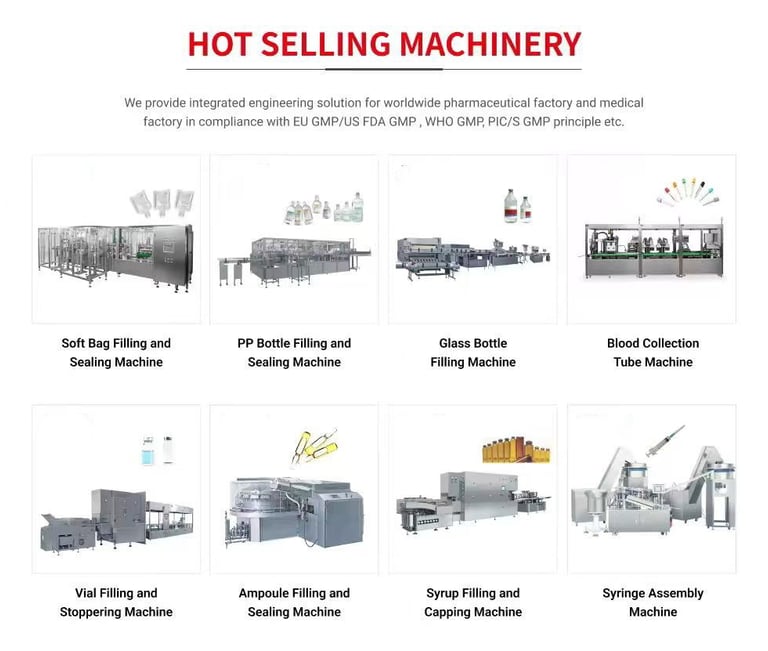
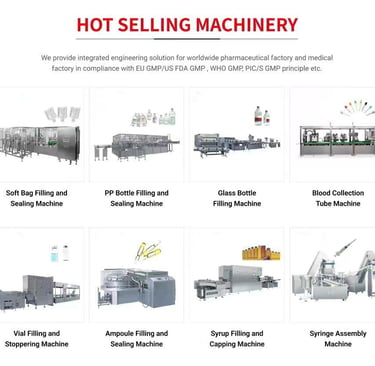