Mastering Heat Dissipation: The Science and Innovation Behind Advanced Thermal Solutions
INDUSTRIAL SUPPLIES
2/8/20254 min read
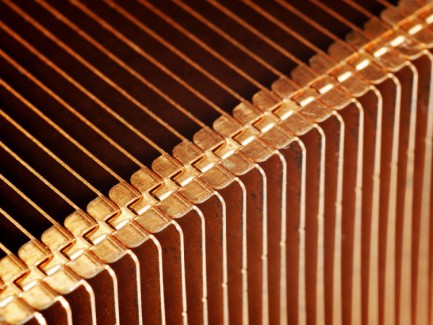
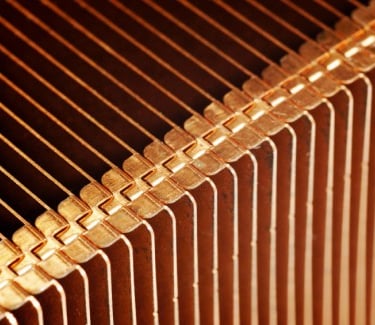
Efficient heat dissipation is the cornerstone of modern engineering, ensuring that electronic components, machinery, and industrial systems operate safely and effectively. Without proper heat management, devices can overheat, leading to performance degradation, reduced lifespan, and even catastrophic failure.
From cutting-edge aluminum extrusions to intricate cold-forged solutions, the evolution of thermal management has unlocked a wide range of innovative techniques. In this comprehensive guide, we delve deep into the core technologies behind advanced heat dissipation, including bonded fins, cold forging, cold plates, die casting, folded fins, heat pipes, skived fins, and snapped fins.
By understanding these methods, manufacturers, engineers, and designers can optimize thermal performance, improve energy efficiency, and enhance product durability.
Aluminum Extrusions: The Foundation of Thermal Management
Aluminum extrusions are a staple in the world of thermal solutions. They are formed by forcing heated aluminum through a die to create precise, intricate cross-sectional shapes.
Why Choose Aluminum Extrusions?
High Thermal Conductivity – Aluminum efficiently transfers heat, making it ideal for heat sinks and cooling systems.
Lightweight & Durable – Its low density ensures that extruded parts remain lightweight without sacrificing strength.
Cost-Effective Manufacturing – The extrusion process allows for high-volume production with minimal material waste.
Customizable Designs – Complex geometries can be achieved, optimizing surface area for maximum heat dissipation.
Applications of Aluminum Extrusions in Cooling Systems
Heat Sinks – Used in electronics, LED lighting, and power modules.
Automotive Cooling Components – Found in radiators and engine heat exchangers.
Industrial Machinery – Essential for managing heat in high-power equipment.
Bonded Fins: Enhancing Heat Sink Performance
Bonded fin heat sinks take aluminum extrusions to the next level by increasing surface area and improving heat dissipation. This method involves bonding thin metal fins to a base plate using high thermal conductivity adhesives or soldering techniques.
Advantages of Bonded Fins
High Surface Area Density – More fins mean more contact with air, leading to efficient cooling.
Material Versatility – Fins can be made of copper or aluminum for optimal thermal performance.
Ideal for High-Performance Cooling – Used in industrial power electronics, avionics, and military applications.
Challenges of Bonded Fin Heat Sinks
Higher Manufacturing Cost – Precision bonding increases production expenses.
Potential Adhesive Limitations – The quality of bonding materials affects long-term reliability.
Cold Forging: Precision and Strength in Heat Dissipation
Cold forging is a metal forming process where a slug of material is compressed at room temperature to create highly durable heat sinks and thermal components.
Why Cold Forging Stands Out
Superior Mechanical Strength – No heat is applied during manufacturing, resulting in strong, defect-free parts.
High Thermal Conductivity – The grain structure remains intact, optimizing heat flow.
Eco-Friendly Process – Generates minimal waste and requires less energy than traditional forging.
Applications of Cold-Forged Heat Sinks
High-Power LED Cooling
Electric Vehicle Battery Thermal Management
5G Base Stations & Communication Equipment
Cold Plates: The Future of Liquid Cooling
Cold plates are advanced thermal solutions designed to transfer heat from critical components using liquid cooling. These plates contain internal channels where coolant flows, absorbing and dissipating heat efficiently.
Benefits of Cold Plates
Exceptional Heat Transfer Efficiency – Liquid cooling outperforms air cooling in high-power applications.
Compact Design – Allows for high-density cooling in constrained spaces.
Reliable Temperature Control – Maintains stable temperatures even under extreme loads.
Where Are Cold Plates Used?
Data Centers & Supercomputers – Essential for maintaining optimal CPU and GPU temperatures.
EV Power Electronics – Keeps batteries and inverters within safe operating limits.
Medical Imaging Equipment – Prevents overheating in MRI and CT scan systems.
Die Casting: Mass Production of High-Performance Cooling Components
Die casting is a manufacturing process that forces molten metal into a mold cavity under high pressure, producing complex, high-precision heat sink designs.
Why Die Casting is Ideal for Thermal Solutions
Scalability – Supports high-volume production with consistent quality.
High Thermal Conductivity – Commonly used materials like aluminum and magnesium enhance heat dissipation.
Design Flexibility – Enables the creation of intricate geometries for optimized cooling.
Industries Benefiting from Die-Cast Heat Sinks
Automotive Electronics
Consumer Electronics & Smartphones
Industrial Automation Systems
Folded Fins: Maximizing Airflow and Heat Exchange
Folded fins involve bending thin sheets of metal into compact, high-surface-area structures that enhance airflow and heat dissipation.
Advantages of Folded Fin Designs
High Fin Density – Improves overall cooling efficiency.
Lightweight Construction – Ideal for aerospace and mobile applications.
Customizable for Different Airflow Directions – Enhances performance in forced and natural convection environments.
Common Uses of Folded Fin Heat Sinks
Aviation & Aerospace Cooling
Military & Defense Electronics
Power Amplifier Heat Management
Heat Pipes: Revolutionary Passive Cooling Technology
Heat pipes are sealed tubes filled with a working fluid that transfers heat via phase change, enabling rapid and efficient heat movement.
Why Heat Pipes Are Game-Changers
Ultra-High Thermal Conductivity – Transfers heat up to 100 times more effectively than solid metals.
Passive Operation – No moving parts, reducing failure rates.
Lightweight & Compact – Ideal for space-constrained applications.
Key Applications of Heat Pipes
Laptops & High-Performance Computing
Aerospace & Satellite Thermal Management
Solar Power & Renewable Energy Systems
Skived Fins: The Ultimate Solution for High-Performance Cooling
Skived fin heat sinks are created by slicing a solid block of metal into thin, continuous fins, maintaining superior thermal conductivity without requiring additional bonding.
Why Skived Fins Are Highly Effective
Seamless Construction – No thermal resistance from joints or adhesives.
Enhanced Heat Dissipation – Higher fin density increases cooling efficiency.
Cost-Effective for Large-Scale Production – Reduces material waste compared to bonded fin solutions.
Where Skived Fin Heat Sinks Excel
Data Center Cooling Systems
Automotive & EV Power Modules
LED Lighting & High-Performance Electronics
Snapped Fins: Precision Engineering for Thermal Management
Snapped fins involve interlocking metal fins into a base plate, creating a highly efficient heat sink without additional adhesives.
What Makes Snapped Fins Unique?
Excellent Mechanical Strength – Rigid design withstands mechanical stress.
Superior Airflow Control – Optimized for both forced and natural convection.
Simplified Manufacturing Process – Reduces costs compared to bonded fin alternatives.
Applications of Snapped Fin Heat Sinks
Industrial Power Supplies
Electric Motor Controllers
Medical Device Cooling
Conclusion
The evolution of thermal management technologies has transformed the efficiency and reliability of modern electronics, machinery, and industrial systems. By leveraging aluminum extrusions, bonded fins, cold forging, cold plates, die casting, folded fins, heat pipes, skived fins, and snapped fins, engineers can design cutting-edge cooling solutions tailored to their specific needs.
As industries continue to demand higher performance and energy efficiency, the future of heat dissipation lies in innovation, precision engineering, and advanced material science.
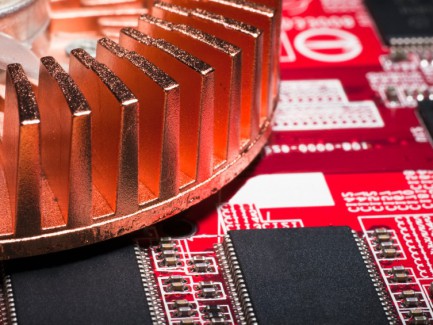
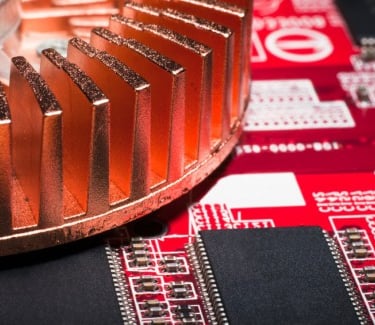