Mastering Hybrid Strategies in Business: From Procurement to Order Fulfillment
SOURCING AGENT
8/19/20248 min read
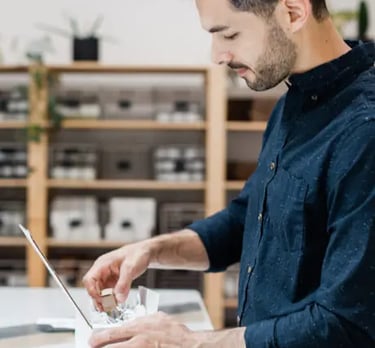
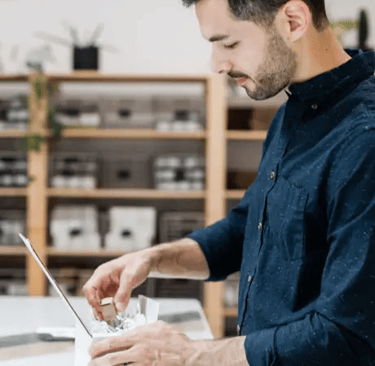
In the dynamic landscape of modern business, companies continuously adapt their strategies to stay competitive and efficient. One such approach that has gained significant traction is the use of hybrid strategies. These hybrid methods blend traditional and modern practices across various functions such as procurement, order fulfillment, and sales processes. In this comprehensive guide, we'll explore the concept of hybrid strategies, including hybrid order fulfillment, hybrid procurement, and more. Let’s dive into the complexities and benefits of these approaches.
What Is a Hybrid Order?
A hybrid order is a type of order that incorporates multiple fulfillment or sourcing methods to meet customer needs efficiently. For instance, a company might combine direct shipments from manufacturers with drop-shipping from wholesalers. This method allows businesses to leverage the strengths of different fulfillment models, ensuring that customers receive their products as quickly and cost-effectively as possible. By utilizing a hybrid approach, businesses can offer a broader range of products while optimizing their supply chain processes.
What Is Hybrid Order Fulfillment?
Hybrid order fulfillment refers to the integration of various fulfillment methods to enhance the efficiency and effectiveness of the order delivery process. This might involve a mix of traditional warehousing and direct-to-customer shipping or a combination of in-house and third-party logistics services. The hybrid approach aims to reduce costs, improve delivery times, and increase customer satisfaction by selecting the most appropriate fulfillment method for each order based on factors such as order size, destination, and product type.
What Is an Example of Order Picking?
Order picking is a crucial step in the order fulfillment process where items are selected from inventory to fulfill customer orders. For example, if a customer orders a set of kitchen appliances, order picking involves retrieving the specific appliances from the warehouse shelves and preparing them for shipment. This process can be done manually by warehouse workers or with the help of automated systems, depending on the complexity and scale of the operation.
What Is the Difference Between Batch Picking and Multi-Order Picking?
Batch picking and multi-order picking are two distinct methods used in warehouse operations to handle order fulfillment:
Batch Picking: This method involves picking items for multiple orders simultaneously. A picker collects items for several orders during one trip through the warehouse. Once all items are collected, they are sorted and packed into individual orders. This method is efficient for high-volume orders where many orders contain similar items.
Multi-Order Picking: In this approach, a picker retrieves items for several orders at the same time but in a more segmented manner. Unlike batch picking, multi-order picking may involve selecting different items for each order simultaneously. This method often uses technology to streamline the process and improve accuracy.
What Is the Hybrid Method of Procurement?
The hybrid method of procurement combines traditional procurement practices with modern techniques to achieve optimal results. For example, a company might use a mix of direct procurement from manufacturers and strategic partnerships with suppliers. This hybrid approach allows businesses to balance cost savings with flexibility and responsiveness, enabling them to adapt to changing market conditions and customer demands more effectively.
What Is Hybrid Sourcing?
Hybrid sourcing is a strategy where a company employs a combination of in-house sourcing and external suppliers to meet its procurement needs. This approach leverages the benefits of both internal capabilities and external resources, providing greater flexibility and efficiency. By using hybrid sourcing, businesses can tap into specialized skills and resources while maintaining control over critical aspects of their supply chain.
What Is the Hybrid Sales Process?
The hybrid sales process integrates different sales methodologies to create a more effective approach. For example, a business might combine direct sales efforts with online sales channels to reach a wider audience. This hybrid approach allows companies to leverage multiple sales avenues, optimizing their reach and increasing their chances of converting leads into customers. By blending various sales techniques, businesses can adapt to changing market conditions and customer preferences more effectively.
What Is a Hybrid Approach in Supply Chain?
A hybrid approach in supply chain management involves combining various supply chain models and practices to create a more resilient and adaptable system. This might include integrating elements of just-in-time (JIT) inventory with safety stock or blending traditional logistics with advanced technologies such as predictive analytics and automation. The goal of a hybrid approach is to enhance supply chain efficiency, flexibility, and responsiveness, allowing businesses to better manage risks and capitalize on opportunities.
What Is the Hybrid Process?
The hybrid process refers to the combination of different processes or methods to achieve a specific objective. In business, this often involves integrating traditional practices with modern techniques to enhance efficiency, effectiveness, or flexibility. For example, a company might use a hybrid process for product development that combines in-house innovation with external partnerships to accelerate time-to-market and improve product quality.
What Skill Is Order Picking?
Order picking requires several key skills, including:
Attention to Detail: Ensuring accurate selection and handling of items.
Organization: Efficiently navigating the warehouse and managing inventory.
Physical Stamina: Handling and lifting items safely.
Time Management: Completing picking tasks within deadlines.
These skills are essential for ensuring that orders are fulfilled accurately and efficiently, contributing to overall customer satisfaction.
What Is Another Name for Order Picking?
Another term for order picking is order selection. This term highlights the process of selecting specific items from inventory to fulfill customer orders, emphasizing the importance of accuracy and efficiency in this critical step of the fulfillment process.
What Is the Principle of Order Picking?
The principle of order picking is to accurately and efficiently retrieve items from inventory to fulfill customer orders. The objective is to minimize errors, reduce picking time, and ensure timely delivery of products. By adhering to these principles, businesses can enhance their order fulfillment processes and improve overall customer satisfaction.
What Is Cluster Order Picking?
Cluster order picking is a method where items for multiple orders are picked simultaneously but grouped into clusters. This approach often uses technology to manage and track multiple orders, enhancing efficiency and reducing picking time. Cluster order picking is particularly useful for high-volume warehouses where many orders contain similar items.
What Is Single Order Picking?
Single order picking is a method where items for one order are picked at a time. The picker retrieves all the items required for a single customer order during one trip through the warehouse. This approach is straightforward and often used in smaller-scale operations or for orders with unique items.
What Is Automated Order Picking?
Automated order picking involves using technology such as robotics, conveyor systems, or automated guided vehicles (AGVs) to retrieve items from inventory. Automated systems can increase efficiency, reduce errors, and lower labor costs by handling repetitive tasks and managing large volumes of orders.
What Is the Hybrid Method?
The hybrid method refers to the use of a combination of different techniques or approaches to achieve a specific goal. In various business contexts, this could mean integrating traditional methods with modern technologies or blending different strategies to optimize performance and outcomes.
What Is a Hybrid Approach?
A hybrid approach involves combining multiple strategies, methods, or systems to create a more effective solution. This approach allows businesses to leverage the strengths of different methods while addressing their individual weaknesses. By adopting a hybrid approach, companies can enhance their adaptability and responsiveness to changing conditions.
What Is a Hybrid PO?
A hybrid purchase order (PO) is a type of order that combines elements from different procurement methods. For example, a hybrid PO might include both standard purchase items and custom-made components, allowing businesses to streamline their procurement processes and better meet their needs.
What Is Hybrid Procurement Structure?
A hybrid procurement structure blends traditional procurement practices with modern approaches. This might involve using a mix of direct procurement, strategic sourcing, and supplier partnerships to achieve optimal results. The hybrid structure allows businesses to balance cost savings with flexibility and responsiveness, enhancing their overall procurement strategy.
What Are the Disadvantages of Hybrid Procurement?
While hybrid procurement offers many benefits, it also has some potential drawbacks:
Complexity: Managing multiple procurement methods can be complex and may require additional resources.
Integration Challenges: Combining different procurement approaches may lead to integration issues and require careful coordination.
Cost: Implementing and maintaining a hybrid procurement structure may involve higher costs compared to a single-method approach.
What Is Hybrid Strategy?
A hybrid strategy involves combining different strategic approaches to achieve business objectives. For example, a company might use a mix of cost leadership and differentiation strategies to compete effectively in the market. The hybrid strategy allows businesses to adapt to changing conditions and leverage multiple strengths.
What Is the Hybrid Methodology Process?
The hybrid methodology process combines elements from different methodologies to create a more effective approach. For instance, in project management, a hybrid methodology might integrate aspects of Agile and Waterfall approaches to address the unique needs of a project. This process allows for greater flexibility and adaptability.
What Is the Hybrid Method of Inventory?
The hybrid method of inventory management combines various inventory management techniques to optimize performance. This might include integrating just-in-time (JIT) inventory with safety stock or using a mix of manual and automated inventory systems. The goal is to balance inventory levels, reduce carrying costs, and improve overall efficiency.
What Is Hybrid Sales Structure?
A hybrid sales structure blends different sales approaches to create a more effective strategy. For example, a business might combine inside sales with outside sales teams to reach a broader audience and optimize sales performance. The hybrid structure allows companies to leverage multiple sales channels and methods.
What Is a Hybrid Logistics Strategy?
A hybrid logistics strategy involves combining different logistics practices to enhance supply chain performance. This might include integrating traditional logistics with advanced technologies such as real-time tracking and automation. The hybrid strategy aims to improve efficiency, reduce costs, and enhance customer satisfaction.
What Is Hybrid Distribution Strategy?
A hybrid distribution strategy combines various distribution methods to optimize product delivery. For example, a company might use a mix of direct-to-consumer shipping and distribution through retail partners. The hybrid approach allows businesses to reach a wider audience and improve distribution efficiency.
What Is a Hybrid Working Strategy?
A hybrid working strategy blends remote and in-office work to create a flexible and effective work environment. This approach allows employees to work from different locations, providing greater flexibility and improving work-life balance. The hybrid working strategy can enhance productivity and employee satisfaction.
What Are Order Picking Methods?
Order picking methods include various techniques used to retrieve items from inventory for order fulfillment. Common methods include:
Single Order Picking: Retrieving items for one order at a time.
Batch Picking: Collecting items for multiple orders simultaneously.
Cluster Picking: Picking items for multiple orders grouped into clusters.
Zone Picking: Dividing the warehouse into zones and assigning pickers to specific zones.
What Is Multi-Order Picking?
Multi-order picking involves retrieving items for multiple orders simultaneously. This method allows pickers to collect items for several orders during one trip through the warehouse, improving efficiency and reducing picking time. Multi-order picking is often used in high-volume operations with similar items across orders.
What Is Sales Order Picking?
Sales order picking is the process of selecting items from inventory to fulfill customer sales orders. This process involves retrieving items based on customer orders and preparing them for shipment. Sales order picking is a critical step in the order fulfillment process and requires accuracy and efficiency.
What Are the Elements of Order Picking?
The key elements of order picking include:
Inventory Management: Ensuring accurate stock levels and item availability.
Picking Techniques: Using appropriate methods such as single order, batch, or multi-order picking.
Accuracy: Ensuring correct items are selected and packed.
Efficiency: Minimizing picking time and optimizing workflows.
What Is Order Picking Metrics?
Order picking metrics are measurements used to evaluate the efficiency and effectiveness of the order picking process. Common metrics include:
Picking Accuracy: The percentage of correctly picked items.
Pick Rate: The number of items picked per unit of time.
Order Fulfillment Time: The time taken to complete an order from picking to shipping.
What Is an Advantage of Order Picking?
The main advantage of order picking is that it ensures accurate and efficient fulfillment of customer orders. By effectively managing the picking process, businesses can reduce errors, improve delivery times, and enhance overall customer satisfaction.
What Are the Hazards of Order Picking?
Order picking can involve several hazards, including:
Physical Injuries: Risks from lifting heavy items or navigating warehouse environments.
Errors: Potential for incorrect item selection or packing.
Efficiency Loss: Challenges in managing high order volumes or complex picking processes.
What Is the Objective of Order Picking?
The objective of order picking is to accurately and efficiently retrieve items from inventory to fulfill customer orders. This process aims to minimize errors, reduce picking time, and ensure timely delivery of products to enhance customer satisfaction.
Is Order Picking Hard?
Order picking can be challenging, particularly in high-volume or complex warehouse environments. It requires physical stamina, attention to detail, and effective time management. However, with proper training, technology, and efficient processes, the challenges can be mitigated to achieve successful order fulfillment.
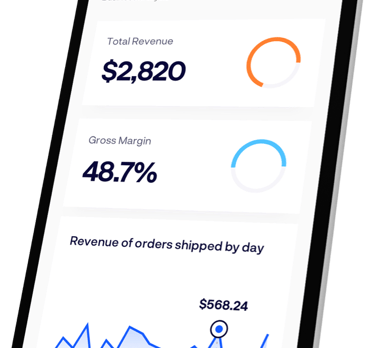
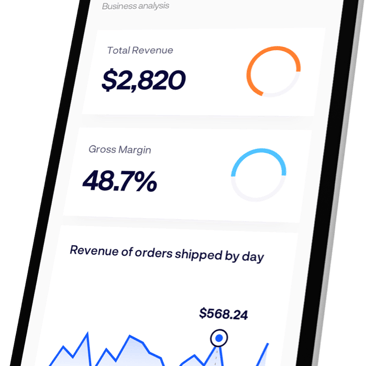