Mastering Wire Processing: The Essential Guide to Crimping, Terminating, and Sourcing Machines
INDUSTRIAL SUPPLIES
12/22/20245 min read
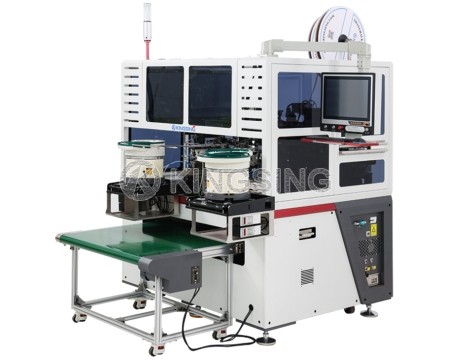
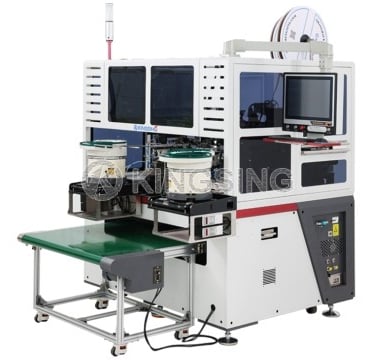
Introduction to Wire Processing Machines: Innovation and Efficiency in Manufacturing
Wire processing is a critical aspect of modern manufacturing, playing a crucial role in industries like automotive, electronics, telecommunications, and appliances. As technology advances, the need for more precise and efficient machines has never been greater. From Cut Strip and Terminate machines to Customized Crimp Machines, the variety of tools available today is impressive, ensuring that every wire, cable, and component is processed to perfection.
As more businesses seek to streamline their operations and reduce costs, sourcing the right machines becomes a key factor in maintaining productivity and quality. Companies like Leon Wholesale, a prominent China Machine Sourcing Agent, help businesses find the best machines for their specific needs, ensuring they meet industry standards and improve overall efficiency. In this blog, we’ll explore the different types of wire processing machines, their functions, and how to choose the right equipment for your manufacturing needs.
Understanding the Importance of Cut, Strip, and Terminate Machines
In wire processing, one of the fundamental tasks is Cutting, Stripping, and Terminating wires. These machines are the backbone of any wire assembly process, ensuring that each wire is accurately cut to length, stripped of its insulation, and terminated with the appropriate connectors.
Cut Strip and Terminate machines are designed to handle a wide range of wire sizes and insulation types, providing consistent results every time. By automating this process, businesses can greatly reduce labor costs, minimize human error, and increase throughput. The ability to handle different wire types and lengths with precision is essential for industries like electronics and automotive manufacturing, where accuracy is paramount.
These machines not only improve productivity but also help ensure the quality of the final product. When sourcing Cut Strip and Terminate machines, it’s important to select a machine that offers flexibility and can handle the complexities of your wire processing requirements.
The Role of Housing/Sleeve Insertion Machines in Wire Assembly
Housing/Sleeve Insertion machines are designed to place a protective sleeve or housing around the wire or connector to prevent wear and tear. This process is vital in applications where wires will be exposed to harsh environments, as the protective sleeve ensures the longevity and safety of the product.
These machines can automate the insertion process, ensuring that the sleeve is placed correctly and securely every time. With Housing/Sleeve Insertion machines, businesses can enhance their wire assembly processes by improving efficiency and reducing manual labor. They’re commonly used in industries such as automotive wiring, where exposure to external factors like heat, moisture, and chemicals is common.
Choosing the right Housing/Sleeve Insertion machine is crucial for ensuring the durability of the final product. It's essential to look for machines that can handle different sleeve types and are adaptable to various wire sizes and materials.
Shrink Tubing Insertion Machines: Securing Wires with Precision
Shrink Tubing Insertion machines are designed to apply heat-shrink tubing to wires and cables, providing an extra layer of insulation and protection. This process is often used in industries like electronics and electrical engineering, where reliable insulation is critical for ensuring safety and performance.
The machine works by feeding the wire through a tube of shrink tubing, which then shrinks when heat is applied, tightly conforming to the wire. This process provides a secure, professional finish while protecting the wire from external elements like moisture, chemicals, and physical damage.
When sourcing Shrink Tubing Insertion machines, businesses should consider factors such as the range of tubing sizes the machine can handle, the speed of the operation, and whether the machine can accommodate various wire types. High-quality machines will ensure that the tubing is applied evenly and securely, preventing any gaps or defects in the insulation.
Exploring the Functionality of Wire Combined Crimping Machines
Wire Combined Crimping machines are designed to simultaneously crimp multiple connectors or terminals onto a single wire, streamlining the production process. These machines are particularly useful in applications where wires need to be connected to multiple terminals at once, such as in automotive harnesses or telecommunications cables.
By automating the crimping process, Wire Combined Crimping machines can increase production efficiency, reduce labor costs, and ensure that each connection is secure and reliable. These machines are capable of handling different types of terminals and wire sizes, offering versatility for a variety of applications.
When sourcing Wire Combined Crimping machines, businesses should focus on the machine’s speed, accuracy, and versatility. Choosing a machine that can accommodate a range of wire sizes and crimping tools will ensure that the crimping process is both efficient and reliable.
Thermal Protector Process: Safeguarding Wires from Overheating
Thermal Protectors are devices that prevent wires and cables from overheating, which can lead to potential fire hazards or damage to the wiring system. Thermal Protector Process machines are used to integrate thermal protection into wires during the manufacturing process, ensuring that the wires remain safe under high temperatures.
These machines typically insert a thermal protection component, such as a thermal fuse or a heat-sensitive coating, into the wire. This added protection is crucial for applications where wires may be exposed to high heat, such as in power distribution or industrial machinery.
Businesses that require Thermal Protector Process machines should consider the types of thermal protection components they need to insert into their wires and ensure that the machine can handle their specific requirements. Reliable Thermal Protector Process machines will improve safety and ensure that wires can withstand extreme conditions without compromising their performance.
Two-Sided Crimp Machines: Precision for Complex Wire Assemblies
Two-Sided Crimp Machines are used for crimping connectors on both sides of a wire, ensuring a strong and secure connection. These machines are particularly useful for applications where a higher level of precision and reliability is required, such as in complex electrical systems or automotive wiring.
By automating the crimping process on both sides of the wire, these machines help reduce the risk of faulty connections and ensure that each crimp is applied with the correct amount of force. This results in stronger, more durable wire assemblies, which are crucial for maintaining the integrity of electrical systems.
When sourcing Two-Sided Crimp Machines, businesses should look for machines that offer adjustable settings, allowing for different crimp sizes and types. High-quality machines will also ensure that the crimping process is fast, efficient, and error-free.
One-Sided Crimp Machines: Simplicity and Efficiency for Basic Applications
One-Sided Crimp Machines are designed to apply crimps to only one side of the wire, making them ideal for simpler wire assemblies. These machines are often used for basic applications, such as connecting single wires to terminals or connectors, and are popular in industries like electronics and consumer goods manufacturing.
Despite their simplicity, One-Sided Crimp Machines are highly effective and can improve production efficiency, reduce labor costs, and maintain consistency in the final product. For businesses with basic crimping needs, these machines are a cost-effective solution that delivers reliable results.
Customized Crimp Machines: Tailored Solutions for Unique Manufacturing Needs
Customized Crimp Machines are designed to meet the specific needs of a business, providing a tailored solution for unique wire processing requirements. These machines can be adjusted to handle different wire sizes, crimp types, and connector styles, ensuring that the crimping process is optimized for each application.
For businesses that require highly specialized crimping processes, Customized Crimp Machines offer flexibility and precision. These machines can be configured to handle unusual or complex wire assembly tasks, providing a level of customization that standard machines cannot offer.
When sourcing Customized Crimp Machines, businesses should work closely with their suppliers to define their specific needs and ensure that the machine is built to meet those requirements.
Conclusion: The Importance of Sourcing the Right Wire Processing Machines
In conclusion, wire processing machines are integral to modern manufacturing, enabling businesses to create high-quality, reliable wire assemblies that meet industry standards. From Cut Strip and Terminate machines to Customized Crimp Machines, each type of machine serves a unique function in the wire processing process.
When sourcing wire processing equipment, businesses should consider factors such as machine versatility, speed, accuracy, and the specific needs of their production processes. Working with a trusted machine sourcing agent like Leon Wholesale can help businesses find the right equipment to improve their operations, reduce costs, and increase efficiency.
By investing in the right machines, businesses can streamline their manufacturing processes, ensure product quality, and remain competitive in a rapidly evolving industry.
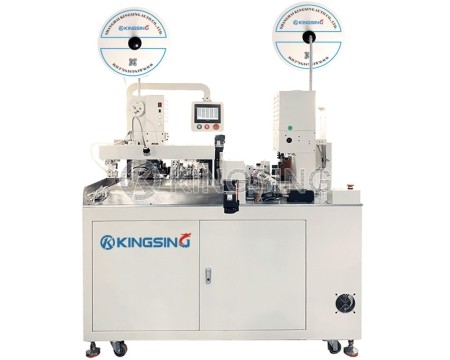
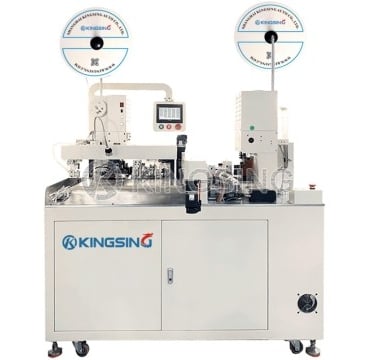