Optimizing Pharmaceutical Safety: Advanced Containment and Sterility Solutions
MEDICAL EQUIPMENT&PRODUCTS
2/9/20253 min read
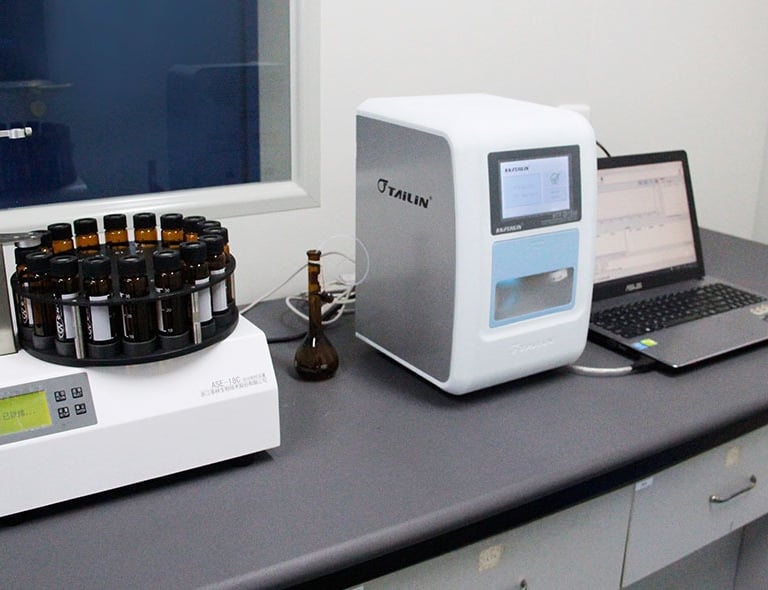
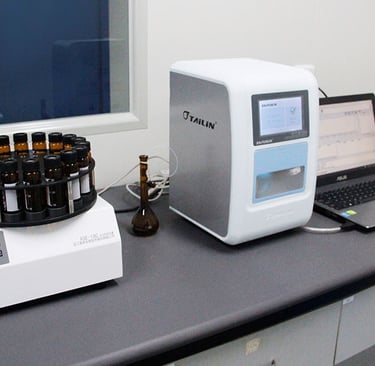
The Role of Pharmaceutical Isolators in Modern Laboratories
Pharmaceutical isolators play a crucial role in maintaining product integrity by providing a controlled and sterile environment. These systems are designed to ensure that sensitive pharmaceutical processes remain uncontaminated, reducing the risk of cross-contamination. Whether in research labs, compounding pharmacies, or production facilities, pharmaceutical isolators serve as a fundamental barrier against microbial and particulate contamination.
Containment Isolators: Ensuring Operator and Product Safety
Containment isolators are specialized systems designed to protect operators and the surrounding environment from hazardous substances. In pharmaceutical manufacturing, handling potent active pharmaceutical ingredients (APIs) requires high-level containment solutions to prevent exposure. These isolators use negative pressure environments and high-efficiency particulate air (HEPA) filtration to ensure safety during drug compounding and production.
Sterile Transfer: Maintaining Purity in Pharmaceutical Processes
Sterile transfer systems facilitate the contamination-free movement of materials between different environments. These systems are vital in pharmaceutical production, ensuring that sterile components, raw materials, and finished products remain uncompromised. Technologies such as rapid transfer ports (RTPs) and sealed container systems provide seamless integration within cleanroom environments.
H2O2 Decontamination: A Gold Standard in Sterility Assurance
Hydrogen peroxide (H2O2) decontamination is widely used for sterilizing isolators, cleanrooms, and critical environments. Vaporized hydrogen peroxide (VHP) technology offers an efficient, residue-free method of decontaminating surfaces and equipment. This technique ensures that microbial contamination is eradicated, providing pharmaceutical manufacturers with a reliable sterility assurance method.
Glove Integrity Tester: Ensuring Contamination-Free Operations
Glove integrity testing is essential for ensuring the safety of isolator systems. Gloves serve as the primary barrier between operators and sterile environments. Regular testing and monitoring help detect leaks, preventing contamination risks. Automated glove integrity testers offer accurate and efficient verification, meeting regulatory compliance requirements.
Sterility Testing: A Critical Step in Pharmaceutical Quality Control
Sterility testing ensures that pharmaceutical products are free from microbial contamination before reaching the market. Utilizing isolators for sterility testing minimizes external interference and enhances test reliability. Closed-loop sterility testing systems provide a contamination-free environment, reducing false-positive results and ensuring product safety.
Sample Pre-Treatment: Preparing for Accurate Microbial Analysis
Before conducting microbiological tests, sample pre-treatment is necessary to remove contaminants and improve accuracy. Advanced pre-treatment systems allow precise handling of samples, maintaining their integrity throughout the analytical process. These systems enhance efficiency and reduce human error in pharmaceutical testing procedures.
Microbial Limit Test: Detecting Contamination in Pharmaceutical Products
The microbial limit test (MLT) assesses the presence of bacteria, yeast, and mold in non-sterile pharmaceutical products. It is a critical quality control step, ensuring compliance with pharmacopeial standards. Using isolators for microbial limit testing enhances accuracy, preventing external contamination that could impact results.
Endoscope Microbial Testing: Ensuring Safe Medical Instrumentation
Endoscope microbial testing is crucial for verifying the sterility of reusable medical instruments. Contaminated endoscopes pose a significant risk of infections in healthcare settings. By employing advanced microbial testing techniques, healthcare providers can ensure patient safety and regulatory compliance.
TOC Analyzer: Measuring Organic Contaminants in Pharmaceutical Water
Total organic carbon (TOC) analysis is a critical quality control parameter for pharmaceutical water systems. TOC analyzers detect organic contaminants that could compromise product safety. These devices play a pivotal role in ensuring that water used in pharmaceutical manufacturing meets stringent purity requirements.
Filter Integrity Testing: Safeguarding Filtration Systems
Filter integrity testing verifies the performance of sterile filtration systems, ensuring they effectively remove contaminants from pharmaceutical products. Pressure decay, bubble point, and diffusion tests are commonly used methods to confirm filter efficiency. Regular testing ensures compliance with Good Manufacturing Practices (GMP) and prevents product failures.
Media Degasser: Optimizing Liquid Chromatography Performance
A media degasser removes dissolved gases from liquid chromatography solvents, enhancing analytical accuracy. In pharmaceutical quality control, degassing prevents bubble formation, which can interfere with instrument performance. These systems improve precision in high-performance liquid chromatography (HPLC) testing, ensuring reliable results.
Conclusion: The Future of Pharmaceutical Containment and Testing
As pharmaceutical industries continue to evolve, the demand for advanced containment, sterility, and testing solutions will grow. Innovations in isolator technology, decontamination methods, and analytical instruments are driving improvements in product safety and regulatory compliance. Investing in state-of-the-art pharmaceutical containment and testing solutions ensures operational efficiency, patient safety, and long-term industry success.

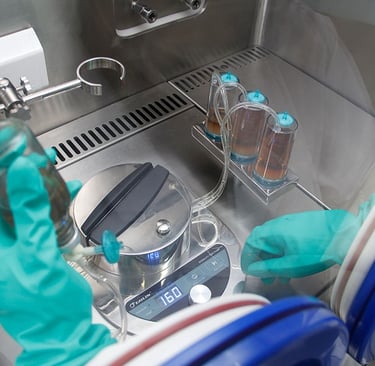