Revolutionizing Busbar Production: Key Machines and Technologies
LEON MACHINERY
4/30/20253 min read
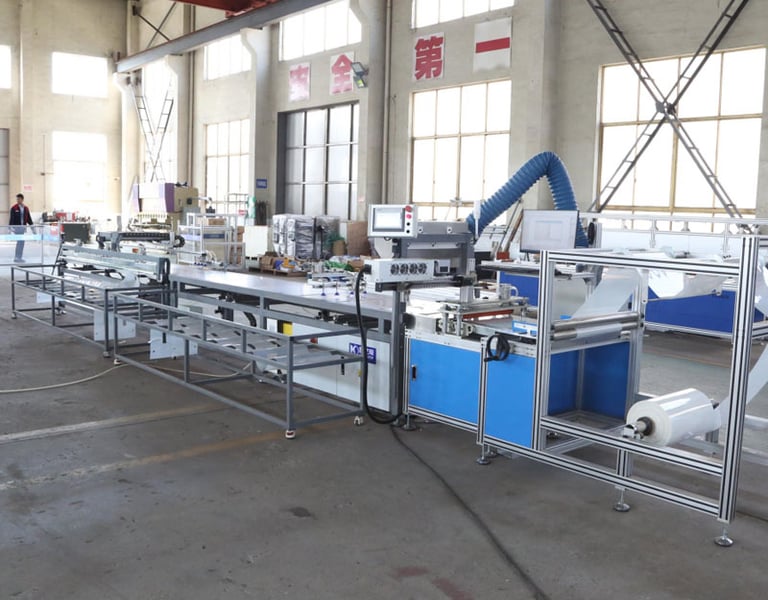
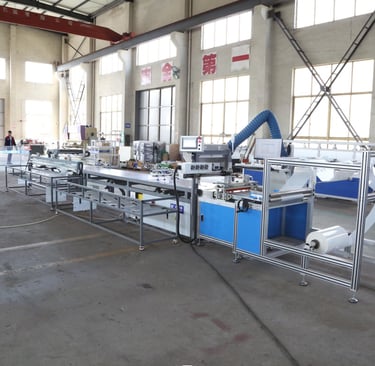
Busbar Machine: The Heart of the Process
At the center of any busbar production line is the busbar processing machine. These machines perform a variety of critical operations such as cutting, punching, bending, and embossing. Modern busbar machines come with programmable logic controllers (PLCs) and human-machine interfaces (HMIs), enabling precision and automation.
They are capable of handling a wide range of conductor sizes and shapes, reducing manual intervention, waste, and error. These machines are indispensable for manufacturers seeking consistency and scalability.
Busduct and Busway Machines: Power Distribution at Scale
Busducts, also known as busways, are enclosed systems that distribute electricity over long distances. Unlike traditional cabling, they are modular, space-efficient, and safer.
To manufacture busducts, specialized busduct machines and busway machines are employed. These systems include housing cutters, enclosure formers, and multi-axis assembly machines. With modular features, they can be quickly retooled for custom sizes and insulation types.
Mylar Film Wrapping Machine
Insulating busbars with Mylar film—a polyester-based film known for its electrical insulation and thermal resistance—is a key step in preventing short circuits and breakdowns.
The Mylar film wrapping machine automates this process by tightly applying layers of insulation around the busbars with precision tension and spacing. This ensures consistent dielectric performance and saves on labor costs.
Mylar Film Slitting Machine
Before wrapping can begin, Mylar film must be prepared in the correct width and thickness. The slitting machine takes large rolls of insulation film and slices them into narrow, even strips. Advanced models offer automatic tension control, edge alignment, and high-speed operation—minimizing waste and downtime.
Welding Robot
Manual welding is a thing of the past in high-throughput environments. A welding robot provides consistent weld quality, speed, and safety. It eliminates human error and fatigue, especially important for thick copper or aluminum busbars that require high heat input.
These robots are equipped with vision systems, path correction algorithms, and AI-based quality checks, ensuring every joint is flawless.
Self-Piercing Riveting Machine
In modern assembly lines, rivets often replace screws and bolts for fastening busbars. The self-piercing riveting machine allows for fast, secure, and vibration-resistant joints without the need for pre-drilled holes. It enhances structural integrity and reduces processing time.
Riveting Machines for Elbow Busbars
When it comes to creating elbow busbars (angled connectors), precision riveting becomes critical. Machines tailored to these unique geometries ensure that angles are preserved and no deformation occurs during fastening.
Automatic Assembly Line
An automatic assembly line integrates various stations—feeding, aligning, welding, riveting, and inspection—into one continuous process. These lines can run 24/7 with minimal supervision, achieving unmatched throughput and repeatability.
They are ideal for large orders with standardized designs, drastically cutting lead times.
Manual Assembly Line
Not all manufacturers need automation. The manual assembly line remains valuable for prototypes, small batches, or highly customized units. Skilled workers assemble components step by step, with quality checks at every stage. Flexibility is the main benefit here.
Automatic Reversal Assembly Line
For designs that require multiple-sided processing or reorientation (such as symmetrical busducts), the automatic reversal assembly line flips and realigns components mid-process. This ensures full coverage without needing separate setups—perfect for complex geometries.
Busway Inspection Machine
Before shipment, every busway must pass through stringent inspections. The busway inspection machine performs:
- Electrical resistance tests
- Dielectric strength checks
- Dimensional accuracy verification
- Visual surface inspections using AI
This guarantees that every unit meets IEC and ANSI standards, preventing costly failures in the field.
Integration of Industry 4.0
Today’s busbar production is no longer isolated. Thanks to Industry 4.0, machines are connected via Industrial IoT (IIoT) networks. Operators can track performance, monitor energy consumption, schedule predictive maintenance, and optimize production schedules from a single dashboard.
Robots communicate with wrapping machines, riveting stations report to central ERPs, and QC systems feed data into AI for defect prediction. This synergy boosts efficiency and enables true smart manufacturing.
Environmental and Economic Benefits
Automated busbar systems are not only faster—they’re greener and more cost-effective. Here's how:
- Reduced scrap rates due to precision cutting and forming
- Lower energy use from smart motors and predictive control systems
- Fewer labor-related errors and occupational hazards
- Sustainable insulation materials like recyclable Mylar and halogen-free polymers
Over time, these advantages translate into lower operating costs and higher ROI.
Choosing the Right Equipment: What to Consider
If you’re planning to invest in busbar manufacturing technology, here are critical factors to evaluate:
- Product range: Do you need to handle copper, aluminum, or both?
- Production volume: High throughput favors automation.
- Customization levels: Manual lines are better for frequent design changes.
- Budget: Robots and smart systems have higher upfront costs but faster payback.
- Footprint: Some automatic lines require more space and power.
Engage with experienced solution providers who offer site surveys, layout design, and after-sales support to ensure your investment delivers long-term value.
Conclusion: Smart Manufacturing, Smarter Future
The age of traditional busbar manufacturing is over. In its place stands a new generation of intelligent, automated systems that are faster, safer, and more adaptive. From Mylar wrapping machines to welding robots, from inspection stations to IIoT dashboards, the future of power distribution is built on innovation.
As global demand for energy continues to climb, and as smart cities and electric vehicles become the norm, manufacturers who embrace these technologies will lead the charge. Don’t get left behind—automate, innovate, and power the future.