Revolutionizing Medical Liquid Bag Production: Innovative Machines and Cutting-Edge Technology
INDUSTRIAL SUPPLIES
11/4/20246 min read
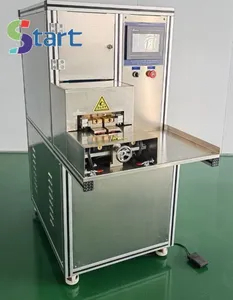
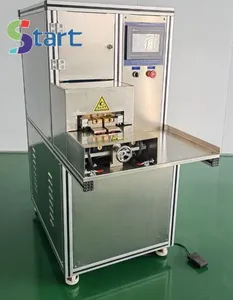
The medical industry constantly seeks ways to improve the efficiency and quality of its manufacturing processes. One critical area of focus is the production of medical liquid bags, which are essential for various healthcare applications, including intravenous (IV) therapy, ostomy bags, and more. The manufacturing of these bags requires precision, reliability, and adherence to strict quality standards to ensure patient safety.
In this blog, we’ll explore the innovative machines that are revolutionizing the production of medical liquid bags. From heat sealing and welding machines to advanced soft bag filling and sealing machines, we’ll examine the latest technology driving efficiency in medical bag production lines. Whether you’re a manufacturer, supplier, or industry enthusiast, this guide will provide valuable insights into how these machines contribute to better, safer medical products.
Understanding the Importance of Medical Liquid Bags
Medical liquid bags are crucial for delivering fluids and medications to patients, providing hydration, nutrition, and medical treatments. They come in various forms, including:
IV Bags: Used for intravenous fluid administration.
Ostomy Bags: Collect waste from patients with ostomies (surgical openings in the abdomen).
Colostomy, Ileostomy, and Urostomy Bags: Specialized bags for individuals who have undergone different types of ostomy surgeries.
The production of these bags requires precision to ensure they are safe, durable, and capable of withstanding the conditions in medical settings. The manufacturing process involves multiple stages, including molding, filling, sealing, and packaging, all of which are critical for ensuring the bags meet health and safety regulations.
Key Equipment for Medical Liquid Bag Production
Several machines are essential for creating high-quality medical liquid bags. These machines are designed to enhance efficiency, reduce production costs, and ensure the final product is safe and reliable. Let's take a look at the most important equipment in the medical liquid bag production line.
Heat Sealing and Welding Machines for Medical Liquid Bags
One of the most crucial machines in medical liquid bag production is the Heat Sealing and Welding Machine. This machine is responsible for sealing the edges of the bags after they have been filled with the necessary medical liquids. Heat sealing ensures that the bags remain sterile and that the liquid does not leak during storage or transportation.
How Does Heat Sealing Work?
The process involves applying controlled heat and pressure to the edges of the plastic film or material used to make the bag. This causes the material to melt slightly and fuse together, creating a strong bond that is capable of withstanding the internal pressure of the liquid. Heat sealing is often followed by additional quality control checks to ensure the seal is secure and meets medical safety standards.
Benefits of Heat Sealing and Welding Machines
Precision and Reliability: Heat sealing machines offer high precision, ensuring that every seal is uniform and reliable. This is particularly important in the medical field, where leaks or defects could compromise patient safety.
Enhanced Sterility: The heat sealing process is effective in maintaining the sterility of medical liquid bags. By fusing the bag material at high temperatures, these machines help create a hermetically sealed environment, minimizing the risk of contamination.
Increased Production Speed: Automated heat sealing machines significantly improve the speed of production, allowing manufacturers to produce large quantities of medical liquid bags quickly without compromising on quality.
Melting Head Ironing Machine Equipment
In addition to sealing, another essential machine in the production of medical liquid bags is the Melting Head Ironing Machine. This machine is used to smooth out and further process the material to create a more uniform and consistent finish. It is typically used in conjunction with other machines, such as those that heat seal or weld the bags, to ensure that the edges are perfectly aligned and finished to the required standards.
How Does the Melting Head Ironing Machine Work?
The Melting Head Ironing Machine applies heat to the material while using a series of rollers or plates to press and smooth the surface. This process not only improves the appearance of the bag but also ensures that the material is evenly distributed. By melting and ironing the material, the machine helps create a seamless, smooth finish that enhances the functionality and aesthetic of the medical liquid bags.
Benefits of Melting Head Ironing Machines
Uniform Finish: The machine provides a consistent, uniform finish across all bags, ensuring that the bags meet aesthetic and functional standards.
Reduced Material Waste: By smoothing the material and preventing defects, the melting head ironing machine helps reduce the amount of waste material generated during production.
Enhanced Durability: The ironing process helps create a stronger and more durable material, reducing the likelihood of issues like tearing or puncturing.
Premium Production Line for Ileostomy, Colostomy, and Urostomy Bags
The production of Ileostomy, Colostomy, and Urostomy Bags requires specialized equipment due to the unique nature of these products. These bags are designed to collect bodily waste from individuals who have undergone ostomy surgeries, and they must be reliable, comfortable, and hygienic. A Premium Production Line is required to meet these specific needs.
Key Components of the Premium Production Line
Automated Bag Forming: Specialized machines form the bags in precise shapes and sizes according to medical specifications.
Filling and Sealing: The bags are filled with specific materials, and their openings are sealed using advanced heat sealing or welding technology.
Quality Control: Automated systems check for defects, such as pinholes, weak seals, or incomplete bags, to ensure that each bag is of the highest quality.
Packaging: After the bags are formed, filled, and sealed, they are automatically packaged for delivery.
Why Premium Production Lines Matter
The production of ostomy bags requires advanced machinery because these bags must meet stringent standards for comfort, durability, and safety. Premium production lines ensure that each bag is perfectly manufactured, minimizing the risk of leakage, discomfort, or other issues that could affect patients' health and quality of life.
Advanced Non-PVC Soft Bag Filling and Sealing Machines
The most advanced technology for manufacturing medical liquid bags involves the Non-PVC Soft Bag Filling and Sealing Machine. These machines are used for creating bags from non-PVC materials, which are preferred for certain medical applications due to their safety and environmental benefits. Non-PVC materials, such as polyurethane, are more flexible, durable, and less likely to leach harmful chemicals into the medical liquid inside.
How Does the Non-PVC Soft Bag Filling and Sealing Machine Work?
This machine combines two key functions: filling and sealing. The soft bag is first filled with a pre-measured amount of medical liquid, and the bag’s opening is sealed through a high-precision process that ensures the bag is leak-proof and sterile. These machines are typically used in high-end medical applications such as IV bags, parenteral nutrition, and other specialized medical treatments.
Benefits of Advanced Non-PVC Soft Bag Filling and Sealing Machines
Environmental Benefits: Non-PVC materials are more sustainable and have a lower environmental impact compared to traditional PVC plastics. They are also less likely to release harmful chemicals when exposed to heat or sunlight.
Improved Patient Safety: Non-PVC bags are less likely to cause adverse reactions in patients, making them ideal for critical applications such as IV therapy.
High Production Capacity: These machines are designed to handle large production volumes, ensuring that manufacturers can meet the growing demand for high-quality, non-PVC medical liquid bags.
The Future of Medical Liquid Bag Production
As the demand for medical liquid bags continues to rise, particularly in emerging markets, manufacturers must adopt the latest technologies to stay competitive. The machines discussed in this blog are at the forefront of innovation, allowing for faster, more efficient, and safer production processes.
The trend toward automation and advanced materials, such as non-PVC plastics, is likely to continue, driven by both regulatory pressures and consumer demand for safer, more sustainable products. The use of sophisticated sealing, filling, and quality control machines ensures that manufacturers can produce high-quality bags at scale while minimizing costs and environmental impact.
Conclusion
The production of medical liquid bags is a complex, highly regulated process that requires precision and efficiency. From heat sealing and welding machines to advanced non-PVC soft bag filling and sealing machines, modern technology has revolutionized the way these essential products are manufactured. As healthcare continues to evolve, so too will the equipment used to produce medical liquid bags, ensuring that they remain safe, reliable, and effective for patient care.
By adopting these advanced production lines, manufacturers can not only meet the increasing demand for medical bags but also ensure that they provide the highest level of safety and comfort for patients around the world. Whether you're in the medical manufacturing industry or a supplier of healthcare products, staying up to date with the latest technologies in medical liquid bag production is essential for success.