Revolutionizing Panel Processing: The Future of Sizing, CNC, and Automation in Modern Manufacturing
LEON MACHINERY
2/7/20256 min read
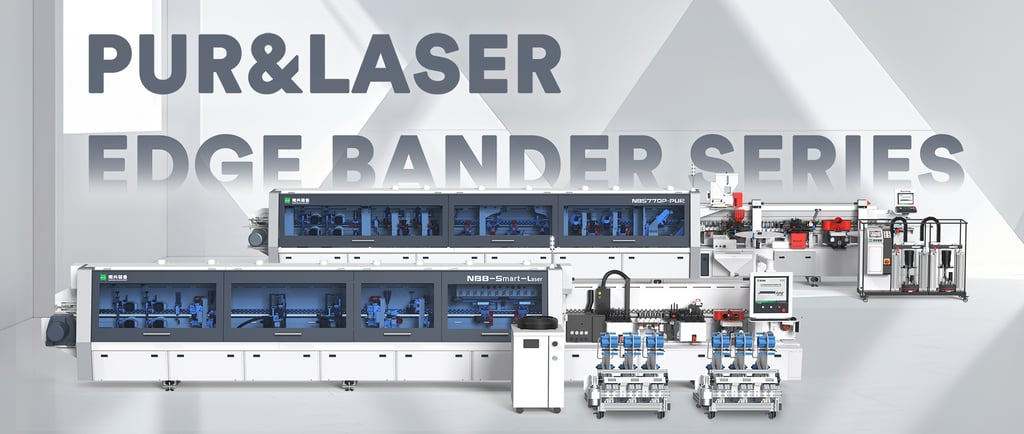
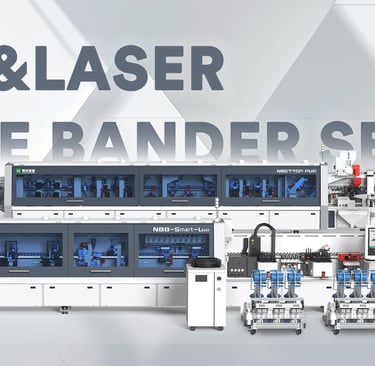
Manufacturing processes are rapidly evolving to meet the growing demand for precision, efficiency, and scalability. In industries such as furniture, cabinetry, and construction, panel processing plays a pivotal role. Panel processing includes cutting, sizing, and finishing materials like wood, MDF, and composites. The machinery and technologies used for these tasks are crucial in streamlining workflows, improving product quality, and minimizing waste.
From advanced panel dividing saws to CNC systems and automation equipment, the landscape of panel processing is continuously evolving. Let’s take a deeper dive into the technologies that are reshaping the future of panel processing, offering unparalleled efficiency and precision.
Understanding the Core Technologies in Panel Processing
Panel processing involves a variety of machines and equipment, each designed for specific tasks. The most common equipment used in panel processing includes panel dividing saws, edge banders, CNC machines, and automation systems. Each of these machines plays an integral role in ensuring high-quality output while improving overall productivity.
Panel Dividing Saw: The Heart of Cutting
The panel dividing saw is one of the most crucial machines in the panel processing industry. This equipment is designed to cut large sheets of material—such as plywood, MDF, or particleboard—into smaller, more manageable panels. There are different types of panel dividing saws, including front-feed and rear-feed models. Front-feed models are typically used for smaller-scale operations, while rear-feed models are designed for higher volume production.
Precision Panel Saw: For Highly Accurate Cuts
For manufacturers who need to maintain strict tolerances, precision panel saws are indispensable. These saws come equipped with digital measuring systems that ensure each cut is accurate to within fractions of a millimeter. This level of precision is particularly important when producing furniture, cabinetry, or components that require exact dimensions. Precision saws not only improve quality but also reduce the likelihood of material wastage.
Specialized Equipment for Advanced Panel Processing
While basic cutting and sizing equipment is essential, certain manufacturing processes demand specialized equipment for more complex tasks like nesting, edge banding, and drilling. These processes require machines that can handle the specific needs of each material and production type.
Nesting Workstations: Optimizing Material Usage
Nesting is the practice of arranging parts to be cut from a large sheet of material in the most efficient way possible. By optimizing the layout, manufacturers can minimize waste and reduce material costs. Nesting workstations utilize both software and CNC technology to generate cutting patterns that maximize the material yield. These systems are especially valuable in industries where material costs are high and sustainability is a priority.
Edge Banding Line: Ensuring Quality Finishes
Edge banding is a critical finishing process in panel manufacturing. It involves applying a protective and aesthetic edge band to the exposed edges of panels. This process is especially common in furniture production, where both appearance and durability are important. Edge banding lines can apply various types of edge material, from PVC to veneer, and some models come equipped with multiple stations for adding glue, applying the edge material, and trimming the edges for a flawless finish.
Drilling Workstation: Precision and Flexibility
Drilling workstations are used to create holes for screws, dowels, and other fasteners required in panel assembly. Modern drilling workstations are often integrated into larger automated production lines. These stations can handle various drilling operations, from simple holes to complex patterns. High-precision drilling machines ensure accuracy and efficiency, reducing the time required for manual adjustments and increasing throughput.
The Role of CNC in Modern Panel Processing
Computer Numerical Control (CNC) technology has revolutionized the manufacturing industry by offering precision, automation, and flexibility. CNC systems are used in a wide range of panel processing operations, from cutting to drilling to shaping. These machines are programmed to perform complex tasks with high levels of accuracy, ensuring consistent results.
CNC Sizing Machines: Streamlining Cutting and Sizing Operations
CNC sizing machines are designed to combine cutting, trimming, and sizing tasks into one integrated system. With CNC controls, operators can input the dimensions and shapes of the panels to be cut, and the machine will execute the cuts automatically. This eliminates human error and increases consistency, making CNC sizing machines ideal for high-volume production.
Five-Axis CNC Machining Centers: Precision Beyond Conventional Limits
For intricate shapes and detailed designs, five-axis CNC machining centers are often the preferred choice. These machines offer five axes of movement, allowing them to process complex cuts, angles, and curves with high precision. Five-axis CNC machines are ideal for creating custom designs or working with irregularly shaped panels. They provide manufacturers with the flexibility to create detailed, intricate patterns that would be impossible with traditional machining methods.
Automation: The Key to Future-Proofing Manufacturing
As demand for faster production and higher-quality products increases, automation has become a key factor in achieving these goals. Automated systems can perform repetitive tasks with precision, reducing labor costs and human error. The integration of automation equipment such as feeder systems, stackers, and conveyors ensures that panels move seamlessly through the production process, from cutting to finishing.
Feeder & Stacker Systems: Streamlining Material Flow
Feeder and stacker systems are essential components of automated panel processing lines. The feeder system automatically loads raw materials into the production line, ensuring that panels are processed without delay. The stacker system is responsible for collecting and stacking finished panels, ready for further processing or shipment. By automating these tasks, manufacturers can speed up production times and reduce reliance on manual labor.
Turner Equipment: Automating Panel Rotation
For panels that need to be processed on both sides, turner equipment is crucial. These systems automatically rotate large or heavy panels, ensuring they are correctly oriented for the next stage of production. Turner equipment improves the efficiency of production lines by eliminating the need for manual handling of large panels.
Conveyor Table Sizing: Continuous Production Flow
Conveyor table systems provide a smooth, continuous flow of materials between different stages of the manufacturing process. Conveyor systems are often used in conjunction with automated feeders and stackers to ensure that panels are efficiently transported from one machine to the next. This allows for a seamless, uninterrupted production process that increases overall efficiency.
Innovations in CNC Drilling and Automation
The integration of advanced CNC technology and automation systems has significantly enhanced drilling operations in panel processing. Drilling machines equipped with CNC capabilities allow manufacturers to achieve higher precision and flexibility, reducing setup times and improving overall productivity.
Through-Feed Drilling Systems: Continuous High-Speed Drilling
Through-feed drilling systems are designed to handle high-speed drilling operations for large volumes of panels. These machines allow panels to pass through continuously, with each hole being drilled precisely according to the programmed parameters. Through-feed drilling systems are particularly useful for applications that require repetitive drilling, such as creating holes for dowels, screws, or hardware.
CNC Drilling Machines: Customizable and Precise
CNC drilling machines are ideal for custom drilling operations. With these systems, manufacturers can create intricate hole patterns for specific components, such as hinges or lock mechanisms. The ability to program drilling operations ensures consistent results, whether the task is as simple as drilling a single hole or as complex as creating an array of holes in a customized pattern.
Door Panel Processing: Specialized Equipment for Unique Needs
The processing of door panels requires specialized equipment that can handle the dimensions, finishes, and durability requirements of these products. Machines like single and dual working tables, along with CNC machines, ensure that door panels are processed efficiently and accurately.
Single and Dual Working Tables: Optimizing Panel Handling
Single and dual working tables are designed to assist in the processing of large door panels. These tables can be equipped with advanced features such as pneumatic lifts, which make it easier to move and position heavy panels for cutting, sanding, or finishing. Dual working tables are particularly useful for manufacturers who require high throughput and the ability to process multiple panels simultaneously.
The Future of Panel Processing: Integration and Smart Manufacturing
As the manufacturing industry continues to evolve, the integration of data-driven technologies and smart systems will play an increasingly important role. Advanced sensors, robotics, and artificial intelligence are expected to improve panel processing operations, making them faster, more efficient, and more flexible.
The future of panel processing is rooted in the integration of machines and systems that can communicate and work together seamlessly. This trend toward smart manufacturing promises to transform the way panel processing companies operate, allowing them to produce higher-quality products faster while reducing costs and waste.
Conclusion: Advancing the Industry with Modern Panel Processing Equipment
The panel processing industry is at a crossroads, with cutting-edge technologies like CNC systems, edge banders, and automated workflows reshaping the way materials are handled and processed. As the demand for higher-quality products and faster production times continues to rise, manufacturers must adapt by embracing these advanced systems. The future of panel processing lies in precision, automation, and integration, and those who invest in these technologies will be well-positioned to lead the industry into the next era of manufacturing.