Revolutionizing Pharmaceutical Production: The Role of Advanced Filling and Capping Machines
INDUSTRIAL SUPPLIES
8/4/20246 min read
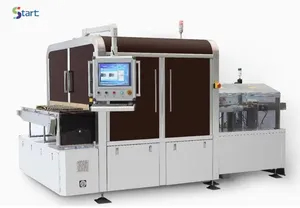
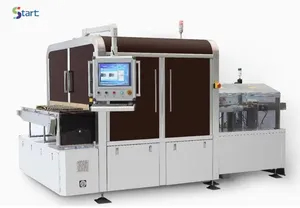
A New Era in Pharmaceutical Manufacturing
The pharmaceutical industry is a vital sector, producing life-saving medications and healthcare solutions for millions of people worldwide. As demand for high-quality, sterile products like ampoules, vials, and blood collection tubes increases, the need for efficient, reliable, and safe manufacturing processes has never been more critical. One of the key innovations that has transformed this sector is the development of advanced filling and capping machines.
These machines are crucial for automating the filling, sealing, and capping of pharmaceutical containers, ensuring that medications remain sterile and effective while meeting stringent industry regulations. In this blog, we’ll explore the cutting-edge technology behind ampoule, vial, blood tube, and other pharmaceutical container filling and capping machines, shedding light on their capabilities, benefits, and how they’re reshaping the pharmaceutical manufacturing landscape.
The Importance of Filling and Capping in Pharmaceutical Production
1. The Complexity of Pharmaceutical Packaging
Packaging is an essential part of pharmaceutical production. It not only protects the contents from contamination but also ensures the integrity of the drug or solution inside. Packaging systems for ampoules, vials, blood tubes, and similar containers require meticulous precision because even the slightest error can compromise sterility, leading to potential health risks.
Filling and capping are two fundamental steps in the packaging process. The filling process ensures that the correct amount of medication is placed inside the container, while the capping process seals the container to maintain sterility and prevent leakage. Advanced filling and capping machines automate both of these processes, significantly enhancing speed, consistency, and accuracy.
2. Meeting Regulatory Standards
The pharmaceutical industry is one of the most regulated industries globally, with stringent standards for product safety, labeling, and packaging. Every batch produced must meet these rigorous standards to ensure the safety of consumers and avoid costly product recalls. Automated filling and capping machines are designed to adhere to these standards by providing high precision and reducing human error, which is critical for maintaining regulatory compliance.
Types of Filling and Capping Machines for Pharmaceutical Packaging
There are various types of filling and capping machines, each designed for specific pharmaceutical containers, such as ampoules, vials, blood collection tubes, and more. Let’s explore these machines in detail:
1. Stoppering and Capping Vacuum Blood Collection Tube Production Machine
Vacuum blood collection tubes are widely used for laboratory testing, diagnostics, and blood storage. The process of filling and capping these tubes is intricate and requires careful attention to detail. The stoppering and capping vacuum blood collection tube production machine combines the functions of both stoppering (sealing the tube) and capping (sealing with a cap) in a single automated process. The machine works with a vacuum system that ensures the blood inside the tube remains uncontaminated, preserving its integrity during transport and storage.
This equipment is essential in ensuring that blood collection tubes are filled with the right amount of vacuum and sealed securely. The use of vacuum ensures that the blood sample is preserved at optimal conditions until it reaches the laboratory for analysis.
2. Advanced Liquid and Powder Vial Filling and Stoppering Equipment
Pharmaceutical vials come in different shapes and sizes, with the need for precise filling to either accommodate liquids or powders. Vial filling and stoppering equipment is designed for both types of substances. The advanced liquid and powder vial filling and stoppering equipment ensures that the correct dosage is filled into each vial while minimizing the risk of contamination.
The machine uses high-speed filling mechanisms and precise stoppering systems to guarantee that the vial’s contents remain uncontaminated. Whether the product is a sterile injectable or a powder for reconstitution, this equipment ensures that both the liquid and powder types are properly filled and sealed, adhering to the highest standards of quality.
3. Advanced Vial Filling and Sealing System for Liquids and Powders
For both liquid and powder-filled vials, sealing is a critical step in ensuring the sterility and safety of the contents. The advanced vial filling and sealing system is designed to handle both types of vials with the utmost precision. After the vial is filled, the system uses specialized sealing mechanisms to hermetically seal the vial, preventing any leakage or contamination.
This system is commonly used for injectable medications, vaccines, and other pharmaceutical products that require high levels of sterility. It also reduces the potential for product wastage due to overfilling or underfilling, which can occur with manual processes.
4. Eyedrop and Vitamin C Bottle Packaging Assembly Machine
For products like eyedrops and vitamin C bottles, the packaging process is more specialized due to the small volume and high sensitivity of the contents. The eyedrop and vitamin C bottle packaging assembly machine is designed to automate the filling, capping, and packaging of these small, delicate bottles. It provides precise control over the filling volume and ensures that each bottle is tightly sealed to maintain the product’s quality.
In the case of eyedrop packaging, this machine ensures that the liquid is filled to the correct level and sealed in a sterile environment. Similarly, for vitamin C bottles, which are sensitive to air and moisture, the capping mechanism is designed to prevent oxidation and preserve the product's potency.
5. Advanced Ampoule Vial Inspection and Leakage Testing Equipment
The ampoule vial inspection and leakage testing equipment is a crucial part of the filling and capping process. Once the ampoules are filled and sealed, it is essential to inspect each one for any defects, such as cracks, improper sealing, or leakage. This equipment uses advanced vision systems and pressure tests to detect even the smallest flaws in the ampoules.
This step is critical in ensuring that the ampoules meet the stringent quality and safety standards required in the pharmaceutical industry. It prevents defective products from reaching the market, ensuring the safety of patients and protecting manufacturers from costly recalls.
6. Advanced Eye Drops Blow-Fill-Seal Machine for Efficient Production
The blow-fill-seal (BFS) technology is one of the most advanced methods for filling and capping small containers such as eye drops. The eye drops blow-fill-seal machine works by forming, filling, and sealing containers in a single, continuous process. This not only increases production efficiency but also reduces the risk of contamination, as the containers are sealed immediately after they are filled.
This type of machine is ideal for high-volume production of sterile eye drops, ensuring that the product remains uncontaminated from start to finish. The BFS technology is especially beneficial in environments where the risk of contamination is high, such as in ophthalmic and other sterile pharmaceutical manufacturing.
7. Advanced Compact Ophthalmic Filling Equipment for Aseptic Packaging
For ophthalmic products, aseptic packaging is a must to maintain the product’s sterility. The compact ophthalmic filling equipment is specifically designed for the precise filling of eye drops and other ophthalmic products, ensuring that the packaging process is carried out in a controlled, sterile environment. This equipment uses advanced filling systems to ensure that the correct volume of liquid is dispensed into each bottle, and the capping system ensures that the bottles are securely sealed to maintain sterility.
The Benefits of Advanced Filling and Capping Machines
1. Enhanced Efficiency and Productivity
The primary benefit of automated filling and capping systems is increased efficiency. These machines can process large quantities of containers in a fraction of the time it would take to do manually. Whether it’s ampoules, vials, or blood collection tubes, automated systems ensure consistent production speeds without compromising quality. This results in higher productivity and faster turnaround times, allowing manufacturers to meet the ever-growing demand for pharmaceutical products.
2. Improved Accuracy and Consistency
Filling and capping are precision tasks, and even a small error can lead to wasted product or contamination. Advanced filling and capping machines eliminate human error by using automated systems that are far more accurate and consistent. These machines are calibrated to fill and cap each container with the exact amount of product needed, reducing the chances of overfilling, underfilling, or other errors.
3. Higher Sterility and Safety Standards
Pharmaceutical products, especially injectables and ophthalmic solutions, must meet strict sterility requirements. Advanced filling and capping machines are designed to operate in controlled, sterile environments. These machines can be equipped with features like cleanroom certification, automated inspection systems, and leak testing equipment, which help ensure that the products are free from contaminants before they are distributed.
4. Regulatory Compliance
In an industry as heavily regulated as pharmaceuticals, compliance with safety standards is non-negotiable. Automated filling and capping machines are built with these regulations in mind, ensuring that the production process is fully compliant with local and international standards. With built-in inspection systems and quality control checks, manufacturers can produce high-quality products that meet regulatory requirements, reducing the risk of costly fines or recalls.
Conclusion: The Future of Pharmaceutical Packaging
The introduction of advanced filling and capping machines has dramatically transformed pharmaceutical production processes. These machines offer numerous benefits, including enhanced efficiency, improved accuracy, higher safety standards, and regulatory compliance. As the pharmaceutical industry continues to evolve, manufacturers are increasingly turning to automation to meet the growing demand for high-quality, sterile products.
The continuous innovation in filling and capping technologies, such as blow-fill-seal systems, ampoule vial inspection equipment, and ophthalmic filling machines, promises to further streamline production and enhance product quality. These advancements will undoubtedly continue to shape the future of pharmaceutical manufacturing, ensuring that patients receive the highest-quality medications in the safest possible packaging.
As the industry moves toward more automated and efficient solutions, the role of these advanced machines will be crucial in driving growth and innovation in pharmaceutical manufacturing.
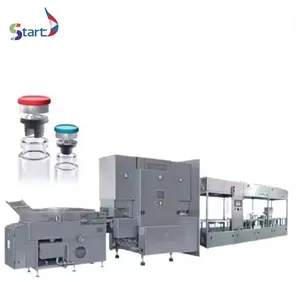
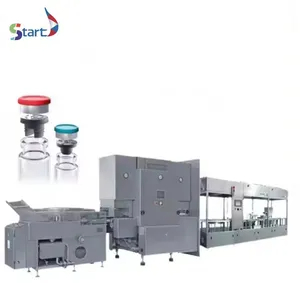