Revolutionizing Quality Control: The Future of Visual Inspection Machines
LEON MACHINERY
1/26/20255 min read
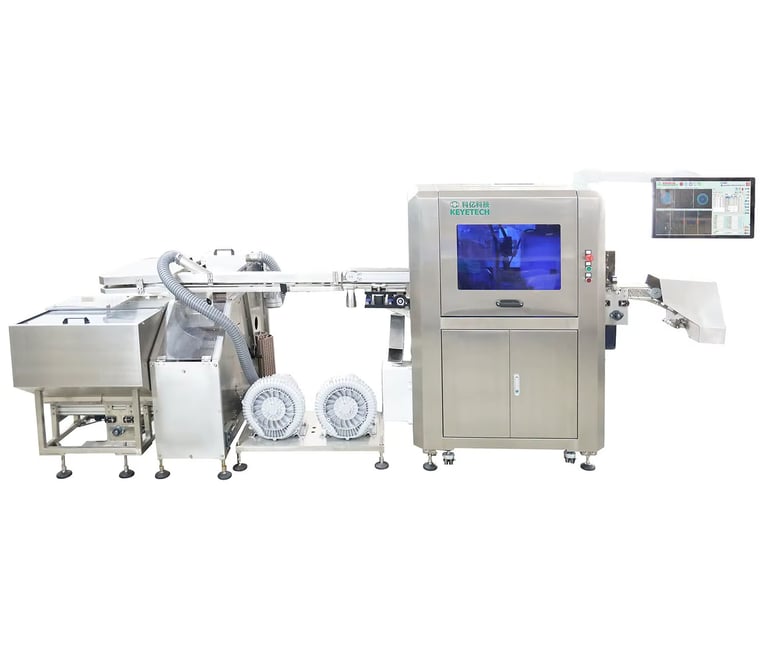
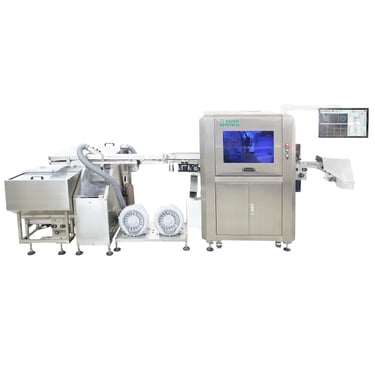
In the world of manufacturing, quality control isn’t just a process—it’s the backbone that ensures products meet the highest standards of excellence. Whether it's ensuring the right fit of a plastic cap, inspecting the clarity of a glass bottle, or analyzing the precision of electronics, visual inspection machines play a crucial role. As industries become increasingly automated, these machines are evolving with the help of artificial intelligence (AI) to meet the growing demand for flawless products.
In this blog, we’ll explore the cutting-edge visual inspection systems for various products, ranging from plastic caps to electronic components, and how these innovations are shaping the future of manufacturing. We’ll dive into the technology behind these machines, their benefits, and how they contribute to a more sustainable and efficient production process.
AI-Powered Visual Inspection Machines: A Game Changer in Quality Control
AI visual defect inspection systems have revolutionized quality control, especially in sectors dealing with high-speed production and large quantities of products. The AI Quality Analyzer is one of the standout innovations in this field. Designed to detect even the smallest defects, it ensures that every product that reaches the consumer is free of imperfections.
But how does it work? At the core of these machines lies machine learning algorithms that continuously improve their detection accuracy. These systems can analyze an image, identify defects, and then make judgments based on pre-programmed criteria. The result? Unparalleled precision in quality assessment.
Plastic Cap Inspection: The Role of AI in Perfection
Plastic cap inspection machines are an essential component of modern manufacturing lines. Often overlooked, the quality of these small, yet crucial, parts can make or break the functionality of an entire product. AI-powered machines now perform a range of tasks, from detecting color inconsistencies to identifying surface imperfections and cracks.
The visual inspection process is automated, meaning faster throughput without compromising on quality. These machines utilize advanced imaging techniques, such as 3D scanning, to create accurate models of the caps. The AI then compares these models against a database of perfect caps, instantly flagging any discrepancies.
Bottles, Bottles, Bottles: Visual Inspection for Plastic and Glass
Whether it’s a plastic bottle used for beverages or a premium glass bottle used for luxury perfumes, the quality of these containers must meet exacting standards. The visual inspection of plastic bottles is crucial for ensuring that they are free from defects such as bubbles, scratches, or improper molding. The same applies to glass bottles, where even minor blemishes can render a product unsellable.
AI visual inspection machines can detect these flaws at speeds that human inspectors could never match. The technology uses high-resolution cameras, sometimes coupled with AI-powered algorithms, to analyze the surface of each bottle. This process ensures that every bottle that leaves the factory is flawless.
IML Inspection: The Silent Hero in Packaging Quality
In-Mold Labeling (IML) has become a preferred method for labeling products in the plastic industry due to its durability and seamless finish. However, inspecting these labels for defects can be tricky. An IML inspection machine, equipped with AI, can detect defects like wrinkles, misalignments, and print quality issues.
The integration of AI in IML inspection machines enhances their efficiency by enabling real-time defect detection. The system can identify issues as soon as they occur, allowing for immediate corrections and minimizing production downtime.
Preform Inspection: Setting the Stage for Perfection
Before plastic bottles are blown into their final shape, the preform (the smaller, molded plastic piece) must be inspected for defects. Preform inspection machines, powered by AI, are responsible for detecting issues such as dimensional inaccuracies, color flaws, or material inconsistencies. Without precise preform inspection, the resulting bottles could suffer from issues like poor sealing or leakage.
With AI, these inspection machines can assess multiple parameters simultaneously, ensuring that each preform meets the required specifications before moving on to the next stage in the production process.
The Integration of AI in Electronics Inspection
It’s not just bottles and caps that require precise inspection. Electronics manufacturing is another area where visual defect inspection machines have proven indispensable. From tiny microchips to larger components, electronic devices must be flawless to ensure their functionality and longevity.
AI-driven visual inspection machines can analyze circuit boards, connectors, and other components for defects like soldering issues, component misalignment, or surface damage. These machines offer a level of scrutiny that’s impossible for human inspectors to match, reducing errors and increasing the reliability of the final product.
More Than Just Bottles: The Versatility of Visual Inspection Machines
While plastic caps, bottles, and electronics are some of the most commonly inspected items, the versatility of visual inspection machines doesn’t end there. The technology has been adapted for a wide variety of products, from paper and plastic containers to labels and straws.
Take the example of paper plastic containers, which are commonly used in the food packaging industry. These containers need to be free of defects like tears, stains, or misprints. With AI-powered visual inspection machines, manufacturers can ensure that each container is perfect before it’s used for packaging food products.
Similarly, labels, whether on bottles, jars, or boxes, must be aligned perfectly and free of printing errors. Label inspection machines, equipped with AI, can detect issues with label positioning, color, and even text clarity, ensuring that products are presented in the best possible way.
Straw Inspection: An Overlooked Necessity
Straws, often seen as a simple and mundane item, are also subjected to rigorous quality control. AI-powered straw visual inspection machines are used to detect defects such as size inconsistencies, cracks, or incorrect shapes. These machines ensure that the straws used in beverage packaging are functional, safe, and aesthetically pleasing.
How Visual Inspection Machines Contribute to Sustainability
In today’s world, sustainability is no longer just a buzzword—it’s a key consideration for all industries. Visual inspection machines play a vital role in helping companies reduce waste and increase efficiency. By catching defects early in the production process, these machines prevent faulty products from being packaged and shipped, thus reducing the likelihood of returns and waste.
Furthermore, AI-driven inspection systems are designed to be energy-efficient, using less power compared to traditional manual inspections. This not only cuts down on operational costs but also helps companies meet their environmental goals.
The Future of Visual Inspection: What’s Next?
As we look ahead, the future of visual inspection machines is bright. The integration of AI is just the beginning. We can expect to see further advancements in machine learning, where inspection systems will not only detect defects but also predict potential issues before they occur. This predictive maintenance capability will help companies proactively address problems and further reduce downtime.
Moreover, as industries adopt Industry 4.0 principles, visual inspection machines will become even more connected, allowing for real-time data analytics and insights. These systems will integrate seamlessly into the broader manufacturing process, creating a more intelligent, automated, and efficient production environment.
Conclusion: Embracing the Future of Quality Control
The evolution of visual inspection machines, particularly those powered by AI, is transforming industries around the globe. From plastic caps to electronic components, these machines are setting new standards in quality control. By ensuring that every product is perfect, manufacturers can reduce waste, improve efficiency, and ultimately provide consumers with better products.
As technology continues to advance, we can only expect these inspection systems to become even more sophisticated, pushing the boundaries of what’s possible in manufacturing. The future is bright, and it’s clear that AI visual inspection machines will be at the forefront of this revolution.
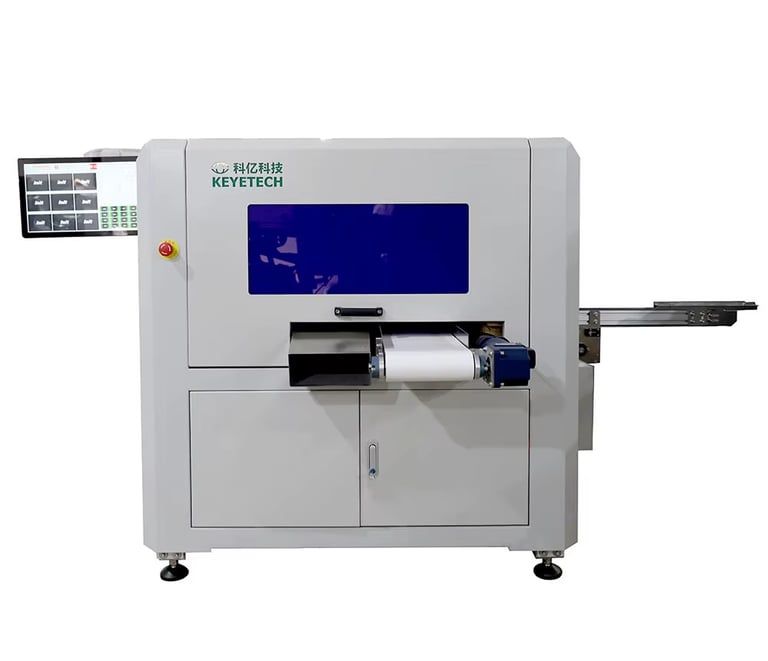
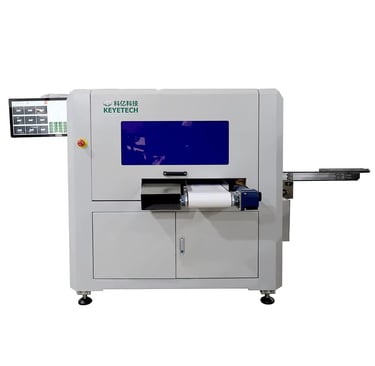