The Complete Guide to Liquid Filling and Packaging Solutions: Unveiling the Latest Technologies and Systems
PHARMACEUTICAL MACHINERY
2/3/20255 min read
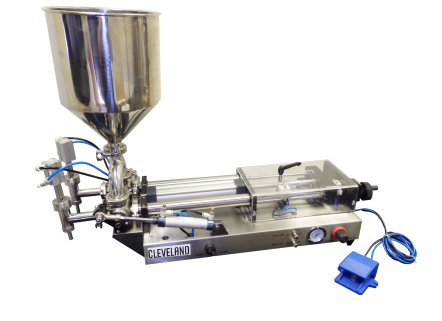
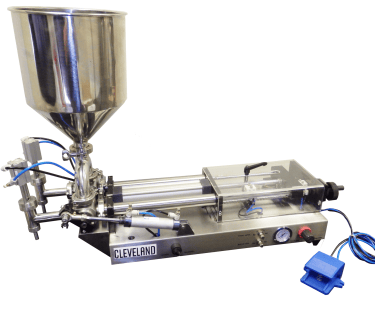
In today's fast-paced production environment, efficient liquid filling and packaging systems are crucial to ensure high-quality products and seamless operations. Whether you're running a small-scale operation or a large manufacturing plant, choosing the right equipment is key to maintaining productivity and meeting demand. In this comprehensive guide, we'll explore a variety of essential liquid filling technologies and systems, from semi-automatic and automatic piston fillers to advanced packaging solutions such as inkjet printers, heat tunnels, and more.
We’ll walk you through the different filling systems, highlighting their uses and benefits, and provide insights into optimizing your production line. Let’s dive into the world of liquid filling machines and the technologies driving packaging innovation.
The Essentials of Liquid Filling Systems
Liquid Filling Machines: The Heart of Packaging
When it comes to liquid packaging, efficiency, precision, and speed are paramount. Liquid filling machines are designed to streamline the process of filling containers with liquids of various viscosities. The choice of filling machine depends largely on the type of product being packaged, its viscosity, and the required filling speed.
Piston Fillers: Accuracy Meets Versatility
Piston fillers are popular in industries that require precision and versatility. These machines are ideal for filling thick, viscous liquids such as oils, sauces, and creams. They operate by using a piston mechanism to draw liquid into a cylinder and then dispensing it into containers.
One of the standout features of piston fillers is their ability to handle a variety of liquid viscosities with precision. This makes them highly suitable for industries like food and beverages, cosmetics, and pharmaceuticals.
Semi-Automatic vs. Automatic Piston Fillers
While both semi-automatic and automatic piston fillers are used for high-precision filling, the key difference lies in the level of automation. Semi-automatic fillers require manual intervention for some aspects of the filling process, whereas automatic piston fillers are fully automated, requiring minimal human involvement.
In high-demand environments, automatic systems are typically preferred due to their speed and consistency. On the other hand, semi-automatic fillers are often more cost-effective for smaller production runs.
Other Liquid Filling Technologies
Siphon Fillers: Ideal for Gravity-Based Systems
Siphon fillers are simple yet effective machines that rely on gravity and the siphon principle for dispensing liquids into containers. These systems are best suited for low-viscosity liquids like water or alcohol. They're particularly advantageous when you need a cost-effective solution for filling large quantities of product at a steady pace.
Gear Fillers: Precise and Consistent
Gear fillers are another excellent choice for filling thicker liquids or products that require highly accurate dosing. They utilize two interlocking gears to draw liquid into the system and dispense it into containers. Gear fillers are ideal for products such as syrups, shampoos, and other viscous liquids. Their precision and consistent output make them a favorite in many industries.
Peristaltic Pumps: Clean and Hygienic Filling
Peristaltic pumps are designed for filling liquids in industries that prioritize hygiene, such as pharmaceuticals and food production. The pump works by squeezing a flexible tube, pushing the liquid through in a controlled manner. Since the liquid never comes into contact with the pump mechanism, peristaltic pumps are highly hygienic and suitable for sterile environments.
Expanding the Packaging Line: More Than Just Filling Machines
While filling machines are crucial, the overall efficiency of your production line relies on complementary packaging technologies. Let’s take a look at other essential equipment that ensures smooth and effective packaging processes.
Automatic Capping Machines: Sealing the Deal
Once the product is filled into containers, capping comes next. Automatic capping machines are designed to cap bottles, jars, and containers of all shapes and sizes with speed and precision. These machines can handle various cap types, from screw caps to flip-top lids, ensuring the final product is securely sealed.
Labeling Solutions: Making Your Product Stand Out
Labeling is another critical step in the packaging process. Automated labeling machines ensure that labels are applied quickly and precisely, providing essential product information while enhancing brand visibility. There are several types of labeling systems, including bottle label applicators, flat label applicators, and shrink sleeve labeling machines. Each offers unique benefits depending on your product’s shape and packaging requirements.
Shrink Tunnels: Perfect for Shrink Sleeve Labels
For products that require shrink sleeves, shrink tunnels are indispensable. These machines use heat to shrink labels tightly around bottles or containers, creating a professional, tamper-evident seal. Heat shrink tunnels are essential for businesses looking to add a layer of protection and visual appeal to their products.
Integrated Packaging Solutions: Streamlining the Entire Process
Packaging isn’t just about individual machines; it's about creating a seamless, integrated system. A compact filling line, combining liquid filling, capping, labeling, and other key processes, ensures that your production runs smoothly and efficiently.
Compact Filling Lines: All-in-One Systems for Efficiency
Compact filling lines combine multiple packaging processes into one streamlined system. These lines typically include liquid filling, capping, labeling, and even sealing, all integrated into one machine or system. Compact filling lines are perfect for businesses with limited space or those looking to automate their entire packaging process with minimal manual intervention.
Conveyors and Rotary Tables: Efficient Product Movement
Conveyors and rotary tables are essential for moving products between different stages of the production process. Conveyor systems allow products to be moved automatically from one machine to another, reducing the need for manual handling and increasing overall efficiency. Rotary tables help align products in preparation for labeling, capping, or sealing.
Packaging Accessories: Supporting the Process
While the main filling and packaging machines are essential, the right accessories can make a big difference in optimizing your production. These accessories include:
Inkjet Printers: Essential for printing batch numbers, expiration dates, and other important information on product packaging.
Heat Shrink Tunnels: For shrink sleeve labels, these tunnels create a tight, tamper-evident seal.
Case Sealers: For sealing packaging boxes quickly and securely, ensuring the contents remain safe during transport.
Pinch Bag Sealers and Bag Sewers: These machines are perfect for sealing bags of various sizes, ensuring a clean and secure closure.
The Future of Liquid Filling and Packaging
As industries continue to evolve, so too do the technologies surrounding liquid filling and packaging. The demand for higher-speed production lines, greater automation, and smarter packaging solutions is increasing.
Innovations like smart sensors, machine learning for predictive maintenance, and even blockchain for traceability are transforming the packaging industry. These technologies are making filling systems not only faster but also more reliable and sustainable.
Conclusion: Choosing the Right Packaging Solution for Your Business
Choosing the right liquid filling and packaging solution is essential for streamlining your production process and ensuring that your products meet customer expectations. Whether you're looking for a semi-automatic piston filler or a fully integrated packaging line, there’s a solution tailored to your needs.
With the variety of filling technologies, capping systems, labeling solutions, and more, it’s easier than ever to build a fully optimized production line. By understanding the different technologies available and their benefits, you can select the best equipment to help your business thrive in the competitive market.
So, which solution will you choose to take your production to the next level?
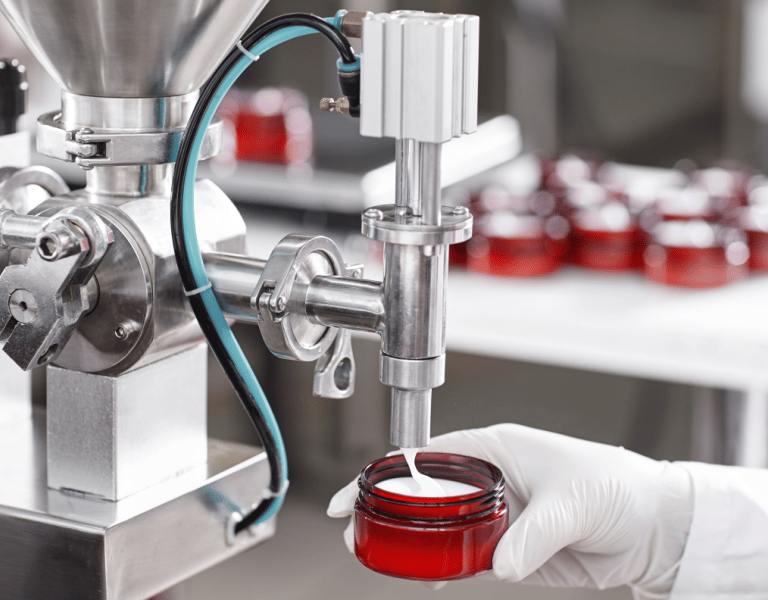
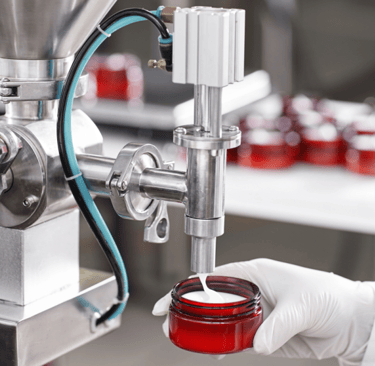