The Ultimate Guide to Industrial Measurement Solutions: Revolutionizing Process Control Across Multiple Industries
INDUSTRIAL SUPPLIES
2/12/20255 min read
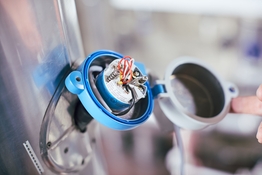
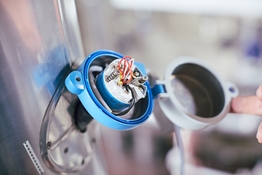
Industrial processes rely heavily on accurate measurements to ensure safety, efficiency, and compliance. With the rapid evolution of technology, the role of advanced sensors, analyzers, and measurement devices has become increasingly important in industries like food and beverage, oil and gas, life sciences, chemical manufacturing, and more.
In this comprehensive guide, we will explore the many facets of industrial measurement solutions, from liquid analysis to level and pressure measurement, and how the latest innovations are transforming operations. We’ll also dive into the importance of sustainability, quality control, and energy management across various sectors. Whether you're looking to upgrade your current measurement systems or implement new technologies, this guide will provide you with the insights you need to make informed decisions.
An Overview of Industrial Measurement Solutions
Industrial measurement solutions play a pivotal role in modernizing processes, improving safety, and driving efficiency. With innovations in measurement technologies such as vortex flowmeters, optical analysis systems, and differential pressure flow measurement, industries are better equipped to handle complex challenges and meet regulatory standards.
These measurement technologies are essential not only for ensuring product quality but also for achieving sustainability goals. Industrial measurement solutions span across various domains, from process monitoring and emission control to fluid measurement and energy efficiency optimization.
Liquid Analysis: Precise Monitoring for Consistency and Quality
Liquid analysis involves the measurement and monitoring of liquid properties in industrial processes. Accurate liquid analysis ensures that critical parameters such as pH, conductivity, turbidity, and oxygen levels are within desired ranges, enabling manufacturers to maintain product quality and compliance with industry regulations.
Sensors such as pH transmitters, turbidity sensors, and dissolved oxygen analyzers are commonly used in water treatment plants, chemical manufacturing, and pharmaceutical applications. These sensors provide real-time data, enabling operators to make adjustments and maintain optimal conditions. By integrating liquid analysis systems with automation software, industries can streamline processes and ensure precise control over production.
Optical Analysis: Bringing Precision to Optical Measurement Systems
Optical analysis is crucial for measuring properties like color, light intensity, and transparency in industrial processes. Technologies like Raman spectroscopic systems, emission monitoring solutions, and process photometers utilize the interaction of light with matter to provide highly accurate measurements. These optical systems are used in industries ranging from pharmaceuticals to food production, ensuring the safety and quality of products.
One key benefit of optical analysis is its ability to monitor processes without direct contact with the material being measured, which is especially valuable for hazardous or high-temperature environments. With the ability to measure specific chemical properties, optical analysis technologies enable better process optimization and faster quality checks.
Flow Measurement: Exploring the Latest Flowmeter Technologies
Flow measurement is fundamental for monitoring and controlling fluid dynamics in industrial systems. From gases and liquids to slurries and powders, understanding flow rates is essential for maintaining system efficiency and preventing costly breakdowns. Modern flowmeters come in a variety of types, each designed for specific applications.
Vortex Flowmeters
Vortex flowmeters are widely used for measuring the flow of gases and liquids in industrial pipelines. They operate based on the principle of vortex shedding, where fluid passing through a pipe causes periodic vortices to form, which can be detected by sensors. These flowmeters are highly accurate, reliable, and capable of measuring a wide range of flow rates, making them ideal for applications in industries like chemical processing, power generation, and HVAC systems.
Thermal Mass Flowmeters
Thermal mass flowmeters measure the flow rate of gases by detecting the change in temperature as the gas passes through a heated sensor. These meters are particularly effective for low-flow applications and are used extensively in industries like oil and gas, pharmaceuticals, and environmental monitoring. Thermal mass flowmeters are also favored for their high accuracy and minimal maintenance requirements.
Differential Pressure Flow Measurement
Differential pressure (DP) flowmeters are one of the most commonly used flow measurement devices in industrial settings. They measure the difference in pressure before and after a constriction in the pipeline, which correlates to the flow rate. DP flowmeters are versatile, cost-effective, and suitable for a wide variety of liquids, gases, and slurries. They are frequently used in water treatment, oil refining, and chemical production.
Level Measurement: Understanding the Various Techniques
Level measurement involves monitoring the height or volume of a substance, typically a liquid, in a tank or vessel. Accurate level measurement ensures that processes run smoothly and helps prevent overflows, leaks, and unsafe conditions.
There are numerous techniques for measuring levels, including guided radar, ultrasonic, and hydrostatic measurements. These methods are ideal for applications in industries like wastewater treatment, food and beverage production, and petrochemical manufacturing.
Radar Level Measurement
Radar level measurement systems use high-frequency radio waves to detect the level of a material. These systems are non-contact, making them ideal for measuring liquids and solids in vessels at high temperatures or pressures. Radar sensors are accurate, reliable, and able to operate in a wide range of challenging environments.
Hydrostatic Level Measurement
Hydrostatic level measurement works by measuring the pressure exerted by a liquid column. The pressure at the bottom of the tank correlates to the height of the liquid, providing an accurate reading. This technique is commonly used in industries such as mining, water treatment, and oil and gas.
Pressure Measurement: Keeping Systems Safe and Efficient
Pressure measurement is essential for monitoring and controlling fluid dynamics in pipelines, tanks, and reactors. Accurate pressure sensors help prevent system failures, optimize energy use, and ensure regulatory compliance.
Pressure transmitters, gauges, and switches are used across industries, from utilities to chemicals and power generation. These sensors can detect changes in pressure, alerting operators to potential issues such as blockages, leaks, or equipment failures before they escalate.
Software and System Products: Leveraging Digital Solutions for Enhanced Performance
Software and digital solutions have revolutionized the way industries manage and monitor measurement systems. Data managers, process indicators, and energy managers help operators optimize processes, improve efficiency, and reduce energy consumption.
Software solutions also enable seamless integration with the Industrial Internet of Things (IIoT), allowing real-time data analysis and predictive maintenance. By harnessing the power of data analytics, industries can enhance decision-making, reduce downtime, and maximize operational efficiency.
Temperature Measurement: The Backbone of Process Control
Temperature measurement is critical for maintaining the stability of industrial processes. Whether it's monitoring the temperature of a fluid, gas, or solid, accurate temperature data ensures that operations remain within safe and optimal ranges. Temperature transmitters, industrial thermometers, and high-temperature sensors are designed to measure temperature in extreme environments, from furnaces and boilers to food processing equipment.
Netilion IIoT: A Game-Changer in Industrial Connectivity
Netilion IIoT is a cutting-edge platform that integrates industrial measurement devices with the Internet of Things (IoT), enabling seamless data exchange and analysis. This digital solution provides real-time insights into processes, allowing businesses to monitor performance, predict maintenance needs, and optimize energy usage.
Netilion IIoT platforms like Netilion Value, Netilion Health, and Netilion Analytics offer tailored solutions for various industrial applications, ensuring businesses can leverage the full potential of their measurement devices.
Featured Industries: Tailored Solutions for Every Sector
Each industry faces unique challenges, which is why industrial measurement solutions must be customized to meet the specific needs of different sectors. Whether it’s ensuring compliance in the food & beverage industry, managing wastewater in municipal systems, or optimizing energy use in oil & gas, the right measurement technologies can drive significant improvements in performance and efficiency.
Sustainability and Compliance: Aligning with Industry Trends
Sustainability is a growing concern across industries, and measurement solutions play a critical role in helping businesses reduce their environmental footprint. From emission monitoring to energy management, advanced sensors and analyzers enable companies to comply with regulations while minimizing waste, energy consumption, and emissions.
Conclusion: The Future of Industrial Measurement Solutions
As industries continue to evolve, so too does the need for more accurate, efficient, and sustainable measurement solutions. By investing in advanced sensor technologies, digital platforms, and automated systems, companies can stay ahead of the curve, enhance product quality, and reduce costs. The future of industrial measurement is digital, and the companies that embrace these innovations will lead the way in efficiency, safety, and sustainability.
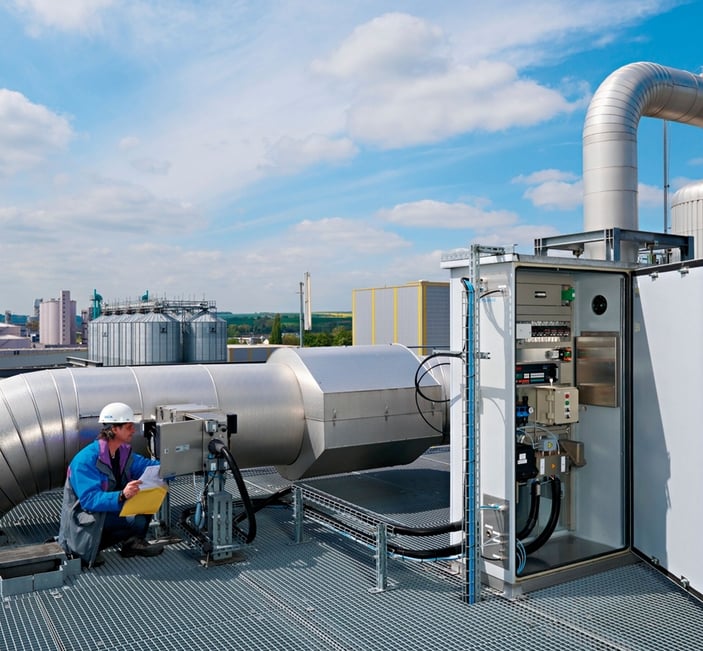
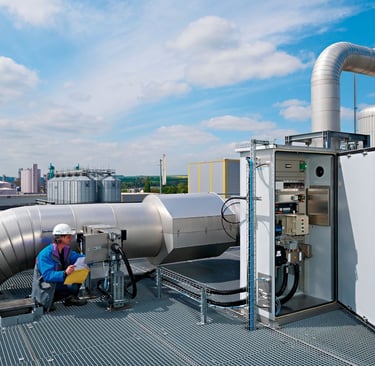