The Ultimate Guide to Water-Based, Oil-Based, and Hot-Melt Adhesives: Which One is Right for You?
INDUSTRIAL SUPPLIES
2/18/20254 min read
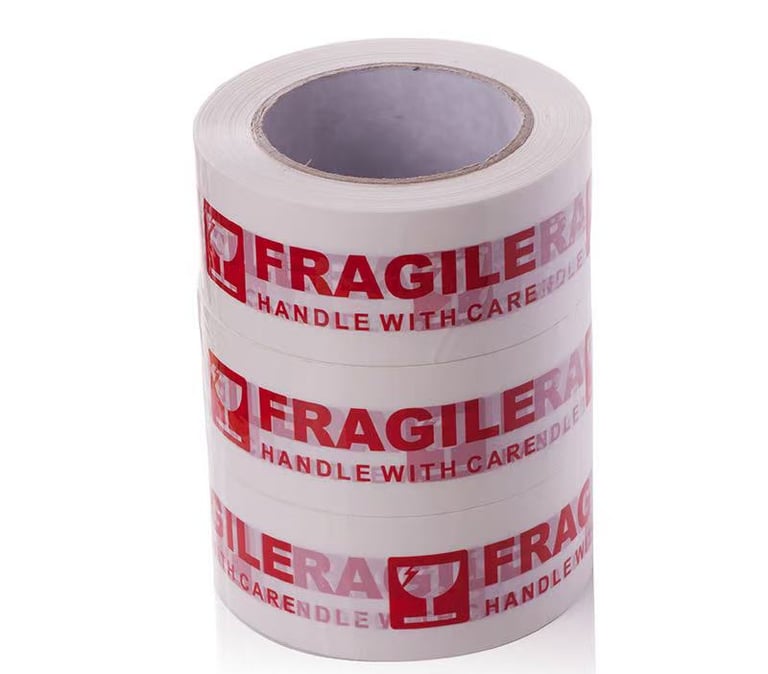
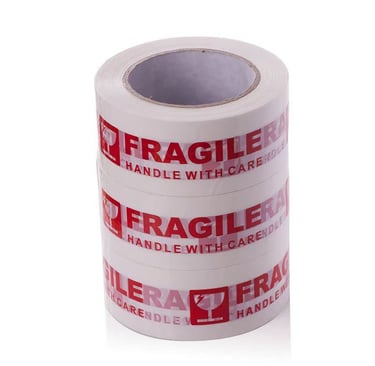
Introduction: Understanding Adhesive Types and Their Importance
Adhesives have become a vital part of both industrial production and daily life. Whether you're assembling products, designing art, or making simple repairs, adhesives are everywhere. However, the world of adhesives is vast, with different types of glue tailored for various purposes. Among these, water-based, oil-based, and hot-melt adhesives stand out as the most commonly used. But how do they compare? Which one suits your needs the best? In this post, we’ll delve into the essential differences, advantages, and disadvantages of these three types of adhesives.
Water-Based Adhesive: Eco-Friendly and Cost-Effective
What is Water-Based Adhesive?
Water-based adhesives use water as a solvent to emulsify acrylic or polyurethane resins, creating a bonding agent that is highly versatile. Often referred to as "aqueous adhesives," these products are popular for a wide range of applications, from paper and cardboard packaging to textiles and wood.
Advantages of Water-Based Adhesives
Environmental Benefits
Water-based adhesives are widely regarded as eco-friendly, primarily because they use water as the solvent. This reduces the need for hazardous chemicals and volatile organic compounds (VOCs), making them safer for both users and the environment.Affordability
Water-based adhesives are generally more cost-effective compared to their counterparts. Their low price point makes them an attractive choice for industries that require high volumes of adhesive, such as packaging and textiles.Safety
These adhesives are non-toxic, odorless, and non-flammable, ensuring safe application, even in confined spaces or environments where health risks are a concern.Versatility
With a wide range of formulations available, water-based adhesives can be used across many different industries, including paper, plastics, textiles, and even automotive applications.
Disadvantages of Water-Based Adhesives
Longer Curing Time
Water-based adhesives generally take longer to cure compared to oil or hot-melt adhesives. While heat can speed up the curing process, it’s not always efficient or possible depending on the material.Weak Water Resistance
Although some water-based adhesives are formulated to be water-resistant, they are not ideal for applications where the bond will be exposed to water regularly.Limited Adhesion on Low-Polar Substrates
Water-based adhesives may struggle to adhere to materials with low polarity, such as certain plastics and non-porous surfaces.
Best Applications for Water-Based Adhesives
Paper and cardboard packaging
Textiles
Woodworking and furniture assembly
Environmental projects requiring non-toxic materials
Oil-Based Adhesive: Superior Bonding Power for Stronger Bonds
What is Oil-Based Adhesive?
Oil-based adhesives utilize organic solvents such as toluene, DMF (dimethylformamide), or ketones to dissolve acrylic or polyurethane resins. These adhesives offer superior bonding strength, making them suitable for applications where durability is paramount.
Advantages of Oil-Based Adhesives
Superior Bonding Strength
Oil-based adhesives excel in terms of bond strength and durability. They form films that offer excellent adhesion to a wide range of materials, even those with low surface energy like plastics and metals.Faster Drying Time
Compared to water-based adhesives, oil-based products typically dry faster, which increases productivity in high-demand manufacturing environments.High Resistance to Environmental Factors
Oil-based adhesives are highly resistant to water, heat, and other harsh environmental factors, which makes them ideal for industries like automotive, electronics, and construction.Broad Application Range
From automotive parts to electronics and metal bonding, oil-based adhesives are used extensively in industries that require strong, long-lasting bonds.
Disadvantages of Oil-Based Adhesives
Environmental and Health Concerns
The solvents in oil-based adhesives can release harmful volatile organic compounds (VOCs), which may contribute to air pollution and pose health risks to workers if not handled properly.Flammability
Many oil-based adhesives are flammable, which raises safety concerns in certain work environments, particularly in manufacturing or processing areas.Longer Ventilation Requirements
Due to the release of VOCs and other gases during application, proper ventilation is essential when using oil-based adhesives.
Best Applications for Oil-Based Adhesives
Automotive manufacturing
Electronics assembly
Metal bonding
Packaging that requires durable bonds
Hot-Melt Adhesive: Instant Bonding for High-Speed Applications
What is Hot-Melt Adhesive?
Hot-melt adhesives are solid materials that melt when heated and return to a solid state once cooled. These adhesives are used primarily in high-speed production processes, such as packaging, labeling, and assembly lines.
Advantages of Hot-Melt Adhesives
Instant Bonding
Hot-melt adhesives create bonds almost immediately once applied. This speed makes them ideal for fast-paced environments, such as packaging or assembly lines.No Need for Drying or Curing
Since hot-melt adhesives do not contain solvents and harden once cooled, they eliminate the need for drying or curing processes, reducing overall production time.Wide Range of Substrates
Hot-melt adhesives bond well to a variety of substrates, including plastics, paper, wood, and metal. Their ability to adhere to many different materials makes them highly versatile.Cost-Effective
The absence of solvents or other liquid ingredients keeps production costs low, and the reduced need for additional curing or drying equipment saves on energy costs.
Disadvantages of Hot-Melt Adhesives
Temperature Sensitivity
Hot-melt adhesives can become brittle or lose their bonding strength at high or low temperatures, making them unsuitable for extreme environmental conditions.Equipment Needs
Applying hot-melt adhesives requires specialized equipment, such as hot glue guns or dispensing systems, which can be costly to maintain.Limited Bonding Strength on Non-Polar Substrates
While they bond well to many materials, hot-melt adhesives may struggle with non-polar substrates like certain plastics or glass.
Best Applications for Hot-Melt Adhesives
Packaging and labeling
Product assembly
Bookbinding
Shoe manufacturing
How to Choose the Right Adhesive for Your Application
Choosing the right adhesive depends on several factors:
Bonding Strength
Consider the strength of the bond you need. If you require a permanent, durable bond, oil-based or hot-melt adhesives may be better options.Environmental Considerations
For eco-conscious projects, water-based adhesives are a more sustainable choice, while oil-based adhesives may not meet environmental standards.Application Speed
If speed is critical to your production process, hot-melt adhesives are ideal due to their quick bonding time.Material Compatibility
Ensure that the adhesive is suitable for the materials you're working with. Oil-based adhesives tend to bond well to metals and plastics, while water-based adhesives are better suited for paper and cardboard.
Conclusion: Which Adhesive is Best for You?
Each type of adhesive—water-based, oil-based, and hot-melt—offers unique advantages and limitations. Water-based adhesives stand out for their environmental friendliness and affordability, while oil-based adhesives are preferred for high-strength bonds and durability. Hot-melt adhesives, on the other hand, offer quick and efficient bonding, making them perfect for high-speed manufacturing processes.
Ultimately, the best adhesive depends on your specific needs, including the materials you're bonding, the required bond strength, and environmental or safety considerations. By understanding the characteristics of each adhesive, you can make an informed decision that enhances your efficiency and product quality.
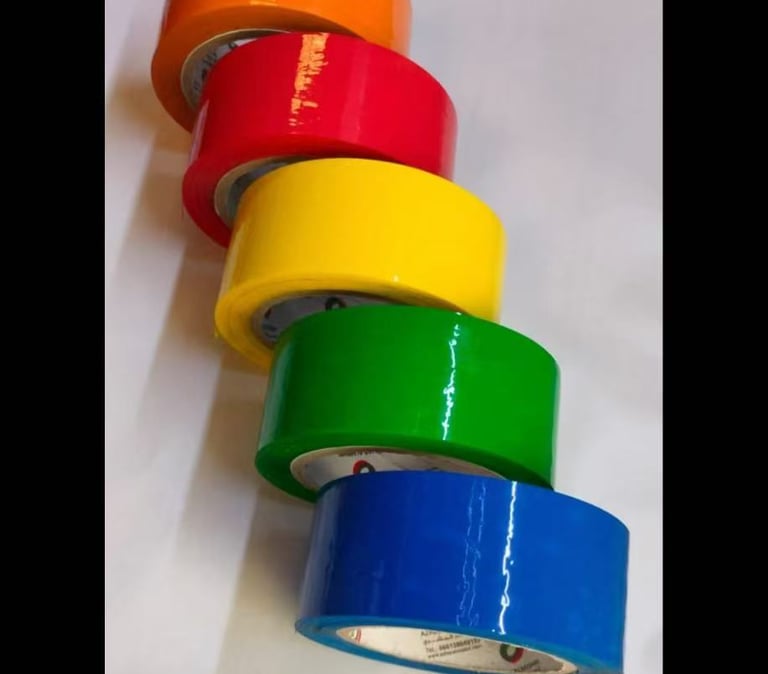
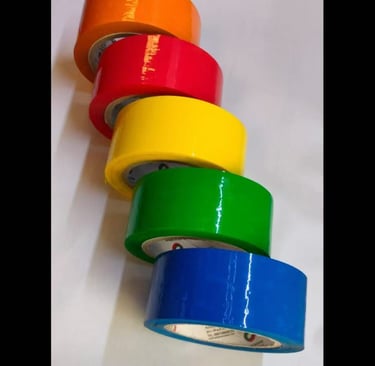