Transforming Syringe Manufacturing with Advanced Production Lines
INDUSTRIAL SUPPLIES
6/5/20246 min read
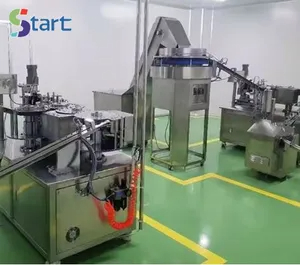
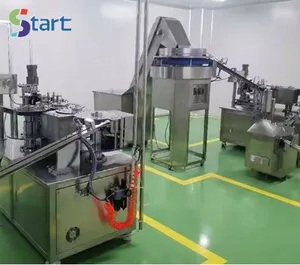
The Evolution of Syringe Manufacturing
In an age where medical technology continues to evolve, the production of syringes has reached new levels of sophistication. As demand for high-quality, safe, and reliable medical devices grows, so does the need for state-of-the-art manufacturing processes. The syringe production line has become a critical part of this transformation, playing an essential role in delivering both the efficiency and precision required for the mass production of syringes and related medical devices.
From insulin syringes to blood collection needles, the syringe production process has become increasingly automated, ensuring that manufacturers can meet strict standards for quality while optimizing production speeds. This blog will explore the various stages and types of syringe production lines available today, highlighting their key technologies, features, and how they are reshaping the medical device manufacturing industry.
The Core Components of a Syringe Production Line
A syringe production line typically involves several steps that are integrated into a seamless process to produce high-quality syringes efficiently. These stages include molding, assembly, printing, packaging, and sterilization. The following sections will outline the critical components of a modern syringe production line.
1. Molding and Injection of Syringe Components
The production process begins with the molding of the syringe’s main components: the barrel, plunger, and needle. Advanced injection molding machines are used to create the syringe barrels, ensuring they meet precise dimensions and are free from defects. These machines are designed for high-volume production, capable of creating hundreds of syringes per hour, which is crucial for meeting market demands.
The self-destructing syringe making machine is another innovation in syringe manufacturing. This machine not only molds the components but also incorporates safety mechanisms that allow the syringe to be automatically deactivated after use. This self-destructing feature is particularly important in preventing needle reuse and ensuring patient safety.
2. Syringe Assembly Machines
Once the individual components are molded, the next step in the production line is assembly. Fully automatic syringe assembly machines are designed to quickly and accurately assemble the components, including the barrel, plunger, and needle. These machines use advanced robotics and precision engineering to ensure that each syringe is assembled to exact specifications, minimizing human error and maximizing efficiency.
High-speed syringe assembly machines are often used in high-demand environments where time is of the essence. These machines can process large quantities of syringes in a short period while maintaining consistency and quality. For more specialized applications, two-part syringe assembly machines are also available, which allow for the assembly of syringes that require more complex structures or additional features.
3. Needle Manufacturing: A Critical Part of Syringe Production
One of the most critical components in syringe manufacturing is the needle. Smart insulin pen needle manufacturing machines have revolutionized the production of insulin delivery devices. These machines provide precise control over the needle’s size, sharpness, and coating, ensuring that the needles are safe and effective for use in diabetes care and other medical treatments.
Additionally, there are hypodermic needle assembly machines, which focus on the creation of general-purpose needles for injections. These machines are designed to produce needles with exacting standards, ensuring smooth operation and patient comfort. As medical advancements continue, the demand for high-quality, reliable needles continues to increase, making efficient needle production essential.
4. Printing and Marking: Adding the Finishing Touches
Once the syringes are assembled, many of them require additional markings, such as product labels, dosage indicators, or brand logos. Syringe roll printing machines are used to apply these markings onto the syringe barrels. These machines can print clear, precise text and symbols that are critical for proper use, ensuring that healthcare providers and patients can read the information easily.
For syringes with specific labeling needs, such as those requiring round face printing, the syringe round face rapid silk-screen printing machine is used. This machine can print on curved or irregular surfaces, ensuring that the labeling process is consistent across a variety of syringe designs. Other specialized machines, such as the centrifugal feeding system silk screen printing machine, are used for specific applications where high-volume, high-precision printing is required.
5. Packaging and Sterilization: Ensuring Safety and Cleanliness
After the syringes have been assembled and labeled, they are ready for packaging. Syringe packaging machines are designed to ensure that the syringes are securely sealed, preventing contamination and damage during storage and transport. These machines can handle various packaging formats, including blister packs, boxes, and bulk containers.
Following packaging, syringes are sterilized to ensure they meet the required safety standards. Autoclaves and other sterilization systems are used to ensure that syringes are free from bacteria and other pathogens. This step is crucial in maintaining the sterility of syringes, particularly for those used in critical medical procedures.
The Benefits of Automation in Syringe Production
As syringe manufacturing processes have become increasingly automated, several advantages have emerged. Automation has helped manufacturers achieve higher efficiency, consistency, and scalability, all of which are essential in a fast-paced, high-demand environment. Some of the key benefits of automated syringe production lines include:
Increased Efficiency: Automated systems, such as fully automatic syringe assembly machines, can operate at higher speeds than manual labor, significantly increasing production output.
Improved Precision: Automated machines ensure that syringes are assembled with greater accuracy, reducing the likelihood of defects or errors in the final product.
Lower Labor Costs: Automation reduces the need for manual labor, cutting down on the costs associated with hiring and training workers, while also minimizing human error.
Enhanced Safety: With features like self-destructing syringes and precise needle manufacturing, automation helps create safer products, reducing the risk of cross-contamination and needle-stick injuries.
Innovations in Syringe Production
The syringe production industry continues to innovate, driven by the demand for higher-quality products and the need for more efficient manufacturing processes. Here are some of the key innovations that are shaping the future of syringe manufacturing:
1. Self-Destructing Syringes
Self-destructing syringes are a breakthrough innovation that addresses the problem of needle reuse, which is a serious safety concern. These syringes are designed to automatically deactivate after use, preventing them from being reused and potentially spreading infections. The self-destructing syringe making machine is specifically designed to incorporate this feature into the production process.
2. Smart Syringes
Smart syringes are another exciting development in the medical device industry. These syringes are equipped with sensors and digital technology that can monitor the delivery of medication, track usage, and even provide feedback to healthcare providers. The smart insulin pen needle manufacturing machine plays a key role in the production of these advanced syringes, allowing for precise control over needle manufacturing.
3. Eco-Friendly Syringes
As the world moves towards more sustainable practices, the syringe industry is also embracing eco-friendly materials and production processes. Manufacturers are exploring biodegradable plastics and other sustainable alternatives to traditional materials used in syringe production.
Challenges in Syringe Production
Despite the many advancements in syringe manufacturing, there are still several challenges that manufacturers must overcome. These challenges include:
Maintaining Quality Standards: As the demand for syringes grows, manufacturers must ensure that their products meet strict quality standards. This requires continuous monitoring and testing of syringes at every stage of production.
Regulatory Compliance: Syringes and other medical devices are subject to stringent regulations set by health authorities such as the FDA. Ensuring compliance with these regulations can be time-consuming and costly.
Cost Pressures: The rising cost of raw materials and labor can impact the profitability of syringe manufacturers. At the same time, the pressure to reduce prices in competitive markets can put additional strain on companies.
The Future of Syringe Production
Looking ahead, the future of syringe production is full of possibilities. With continued advances in automation, smart technology, and sustainable materials, syringe manufacturers will be better equipped to meet the growing demand for high-quality medical devices. The key to success will be embracing new technologies while maintaining a strong focus on safety, efficiency, and cost-effectiveness.
Conclusion
The syringe production line has come a long way from its early days of manual assembly. Today, advanced machinery such as fully automatic syringe assembly machines, syringe printing machines, and smart insulin pen needle manufacturing machines are transforming the way syringes are made. These innovations not only improve the efficiency of production but also enhance the safety and performance of syringes, ensuring that patients receive the best possible care.
As the global demand for medical devices continues to grow, the syringe production industry will need to adapt and innovate to keep pace. By embracing automation, new materials, and advanced technologies, manufacturers can stay competitive in this rapidly evolving market and continue to deliver high-quality products to healthcare providers around the world.
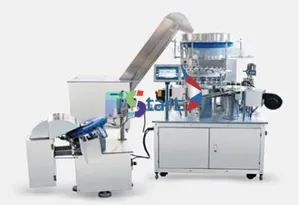
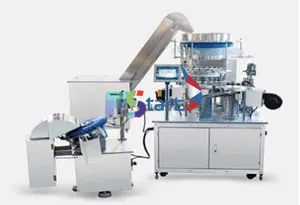