Ultrasonic Transducer: The Heart of Ultrasonic Technology
INDUSTRIAL SUPPLIES
7/21/20246 min read
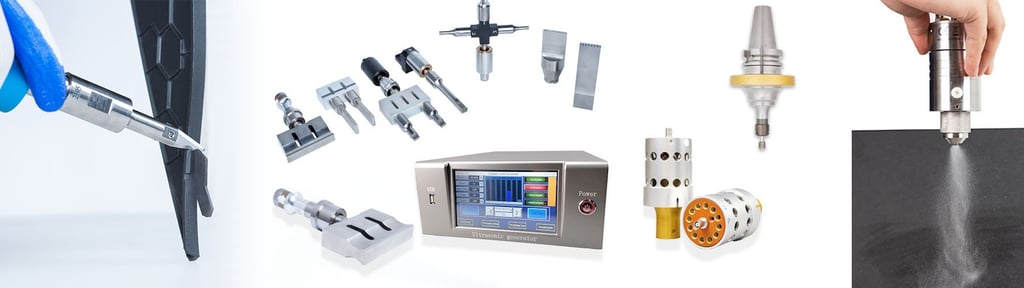
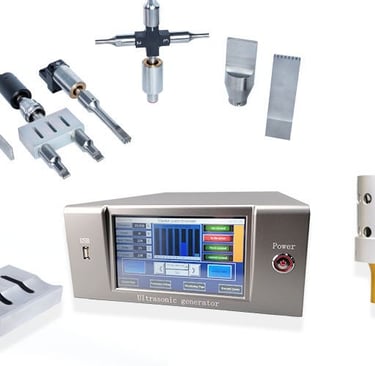
The ultrasonic transducer is the core component of any ultrasonic system. It converts electrical energy into high-frequency sound waves, which are then used in various applications. Transducers are essential in creating the precise vibrations needed for tasks such as welding, cleaning, and cutting. These devices come in different shapes and sizes, tailored to specific applications. For example, in ultrasonic welding, the transducer's performance directly impacts the quality and strength of the welds. The efficiency of an ultrasonic cleaner, on the other hand, relies on the transducer's ability to produce consistent, powerful waves that can penetrate and clean intricate surfaces. Understanding the nuances of ultrasonic transducers is key to leveraging the full potential of ultrasonic technology.
Ultrasonic Welding Machine: Revolutionizing Manufacturing
Ultrasonic welding machines are transforming manufacturing processes across various industries. By using high-frequency ultrasonic vibrations to create heat, these machines weld thermoplastic materials without the need for additional adhesives or solvents. This method is not only faster and more efficient but also environmentally friendly. Ultrasonic welding machines come in various models, each designed for specific applications. Some are compact and portable, ideal for small-scale operations, while others are robust and capable of handling large, complex assemblies. The precision and control offered by ultrasonic welding make it an indispensable tool in industries such as automotive, electronics, and medical device manufacturing.
Ultrasonic Sewing Machine: Innovation in Textile Manufacturing
The ultrasonic sewing machine represents a significant advancement in textile manufacturing. Unlike traditional sewing machines that use needles and thread, ultrasonic sewing machines use ultrasonic vibrations to bond fabrics together. This method produces strong, durable seams without puncturing the material, making it ideal for nonwoven fabrics and delicate textiles. Ultrasonic sewing is also faster and more cost-effective, as it eliminates the need for thread and reduces maintenance. Additionally, the process is cleaner, as it generates less dust and waste compared to conventional sewing. The versatility of ultrasonic sewing machines allows for a wide range of applications, from clothing and upholstery to medical textiles and filtration materials.
Ultrasonic Sealing and Cutting Machine: Precision and Efficiency
Ultrasonic sealing and cutting machines offer unparalleled precision and efficiency in handling various materials. These machines utilize ultrasonic vibrations to generate heat at the point of contact, enabling them to seal or cut through materials with minimal effort. This technology is widely used in packaging, where it ensures airtight seals and clean cuts, enhancing product integrity and shelf life. Ultrasonic sealing and cutting are also popular in the textile and automotive industries, where they provide high-quality finishes without fraying or damage. The ability to precisely control the temperature and pressure during the process makes ultrasonic sealing and cutting machines an invaluable asset in any production line.
Ultrasonic Machining: Advanced Material Processing
Ultrasonic machining is a sophisticated technique used to process hard and brittle materials such as ceramics, glass, and composites. This method employs high-frequency ultrasonic vibrations to remove material from the workpiece, achieving intricate shapes and fine details that are difficult to attain with traditional machining methods. Ultrasonic machining is non-thermal, non-chemical, and non-electrical, making it suitable for delicate and precise applications. It is widely used in industries such as aerospace, electronics, and medical devices, where precision and material integrity are paramount. The ability to machine complex geometries with minimal tool wear and low operating costs makes ultrasonic machining a preferred choice for advanced material processing.
Ultrasonic Cutting Machine: Versatile and Efficient
Ultrasonic cutting machines are designed to handle a wide range of materials with precision and efficiency. By using ultrasonic vibrations, these machines can cut through fabrics, foams, plastics, and composites cleanly and accurately. This method is particularly beneficial for materials that are difficult to cut with traditional blades, as the ultrasonic vibrations reduce friction and prevent material deformation. Ultrasonic cutting is widely used in industries such as textiles, packaging, and automotive, where it provides high-quality cuts with minimal waste. The versatility of ultrasonic cutting machines allows them to be used in various applications, from cutting intricate patterns in textiles to trimming excess material from molded parts.
Ultrasonic Homogenizer: Enhancing Chemical Processes
An ultrasonic homogenizer is a powerful tool used to enhance chemical processes by breaking down particles and emulsifying mixtures. This device uses ultrasonic waves to create intense shear forces, which disrupt cell structures, mix immiscible liquids, and disperse nanoparticles. Ultrasonic homogenizers are widely used in industries such as pharmaceuticals, cosmetics, and food processing, where they improve product quality and consistency. The ability to precisely control the energy input and processing time allows for tailored results, making ultrasonic homogenizers ideal for both laboratory research and large-scale production. Their efficiency and effectiveness in reducing particle size and creating stable emulsions make them indispensable in modern chemical processing.
Ultrasonic Generator: Powering Ultrasonic Systems
The ultrasonic generator is the backbone of any ultrasonic system, converting electrical energy into the high-frequency signals required to drive ultrasonic transducers. This component is crucial for maintaining the stability and efficiency of ultrasonic applications, whether in welding, cleaning, or machining. Ultrasonic generators come with various features, such as frequency tuning, amplitude control, and real-time monitoring, to ensure optimal performance. Advanced models also include digital interfaces and programmable settings, allowing users to customize the ultrasonic output for specific applications. The reliability and precision of ultrasonic generators are essential for achieving consistent and high-quality results in any ultrasonic process.
Ultrasonic Parts: Critical Components for Precision
Ultrasonic parts, including horns, boosters, and fixtures, play a vital role in the effectiveness and efficiency of ultrasonic systems. Each component must be precisely designed and manufactured to ensure optimal performance. The horn, or sonotrode, is responsible for transmitting ultrasonic energy to the workpiece, and its shape and material must be tailored to the specific application. Boosters amplify the ultrasonic energy, enhancing the system's overall efficiency. Fixtures hold the workpieces in place, ensuring accurate and consistent results. High-quality ultrasonic parts are essential for maintaining the reliability and longevity of ultrasonic equipment, and their design and manufacturing require meticulous attention to detail.
Measuring Equipment: Ensuring Accuracy and Quality
Accurate measurement is crucial in any manufacturing process, and ultrasonic systems are no exception. Measuring equipment, such as ultrasonic thickness gauges and flaw detectors, ensures the precision and quality of ultrasonic applications. Thickness gauges use ultrasonic waves to measure the thickness of materials, providing essential data for quality control and inspection. Flaw detectors identify internal defects in materials, ensuring the integrity and safety of the final products. These tools are widely used in industries such as aerospace, automotive, and construction, where precision and reliability are paramount. Advanced measuring equipment enhances the accuracy and efficiency of ultrasonic systems, contributing to overall product quality and consistency.
Ultrasonic Atomization: Innovative Liquid Processing
Ultrasonic atomization is an innovative process used to create fine droplets from liquids, which is essential in applications such as spray drying, coating, and humidification. This method employs ultrasonic waves to generate high-frequency vibrations, breaking the liquid into tiny droplets. Ultrasonic atomization is highly efficient and produces uniform droplet sizes, making it ideal for precise and controlled applications. It is widely used in industries such as pharmaceuticals, food processing, and electronics, where consistent and high-quality atomization is required. The ability to control droplet size and distribution enhances product performance and quality, making ultrasonic atomization a valuable technology in modern manufacturing processes.
Ultrasonic Cleaner: Effective and Gentle Cleaning
Ultrasonic cleaners provide an effective and gentle method for cleaning intricate and delicate items. These devices use ultrasonic waves to create cavitation bubbles in a cleaning solution, which implode and remove contaminants from surfaces. Ultrasonic cleaning is widely used in industries such as jewelry, electronics, and healthcare, where traditional cleaning methods may damage sensitive items. The ability to clean hard-to-reach areas and intricate surfaces makes ultrasonic cleaners ideal for removing dirt, grease, and residues from complex parts. Additionally, ultrasonic cleaning is environmentally friendly, as it reduces the need for harsh chemicals and minimizes waste. The efficiency and effectiveness of ultrasonic cleaners make them an essential tool in maintaining the cleanliness and functionality of various items.
Ultrasonic Welder Repair: Maintaining Peak Performance
Regular maintenance and repair are crucial for ensuring the peak performance of ultrasonic welders. Over time, components such as transducers, horns, and generators may wear out or become damaged, affecting the efficiency and reliability of the welding process. Professional repair services can diagnose and fix issues, replacing worn parts and calibrating the system to restore optimal performance. Regular maintenance also involves cleaning and inspecting components, ensuring they are free from contaminants and in good working condition. Keeping ultrasonic welders in top shape not only extends their lifespan but also ensures consistent and high-quality welds, contributing to overall production efficiency and reliability.
Nonwoven Products Complete Machine: Comprehensive Solutions
Nonwoven products complete machines provide comprehensive solutions for manufacturing nonwoven materials used in various applications such as hygiene products, medical supplies, and filtration systems. These machines integrate multiple processes, including web formation, bonding, and finishing, to produce high-quality nonwoven materials. Ultrasonic technology plays a significant role in bonding and finishing, offering efficient and reliable methods for creating strong and durable nonwoven fabrics. The ability to customize machine settings for specific applications ensures optimal performance and product quality. Nonwoven products complete machines are essential for meeting the growing demand for high-performance nonwoven materials in various industries.