Efficient Conveyor Systems for Streamlined Operations: Unlocking the Power of Automation
LEON MACHINERY
2/22/20254 min read
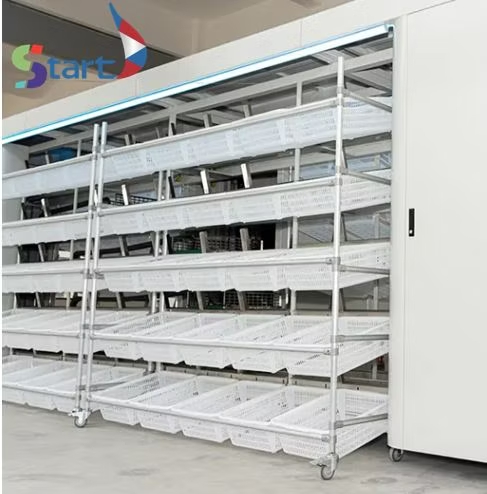
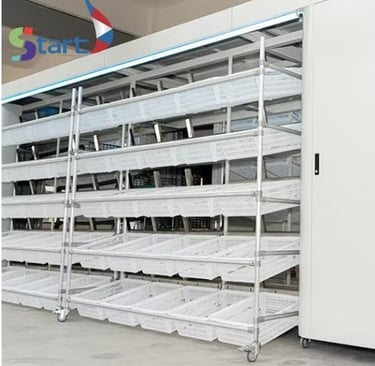
Introduction to Conveyor Systems
In today’s fast-paced manufacturing and logistics industries, conveyor systems are indispensable. They are the backbone of automation, ensuring that goods move swiftly and efficiently through production lines, warehouses, and distribution centers. From small items to heavy pallets, the right conveyor can make a world of difference in operational efficiency.
Among the various types of conveyors, each designed to serve unique needs, the most commonly used include belt conveyors, roller conveyors, chain conveyors, and pallet conveyors. These systems, along with specialized components like roller curves, turntables, and turnouts, provide unmatched flexibility and speed.
But what makes conveyor systems so integral to modern-day industries? Let’s dive deep into the different types of conveyors and explore how they work to revolutionize business operations.
Belt Conveyors: The Industry Standard
Belt conveyors are perhaps the most commonly recognized type of conveyor system. These systems use a continuous loop of material, typically rubber or PVC, to move goods from one point to another. Simple in design, yet highly effective, belt conveyors are used in a variety of industries, including food processing, electronics manufacturing, and parcel handling.
One of the major advantages of belt conveyors is their ability to carry products across long distances with minimal friction. Their flat surface provides a stable platform for items to travel across, ensuring a smooth and consistent flow.
Roller Conveyors: Versatility at Its Best
When it comes to moving items of various shapes and sizes, roller conveyors offer exceptional versatility. These conveyors rely on a series of rollers placed within a frame, which help move products via gravity or powered systems.
What sets roller conveyors apart is their adaptability. Unlike belt conveyors, which are best for uniform products, roller conveyors can handle irregular shapes, making them ideal for applications such as assembly lines and sorting systems. Roller conveyors are also great for heavy-duty tasks, as they can support large and bulky items without compromising efficiency.
Inclined Roller Conveyors: Elevating Your Workflow
When your workflow requires a vertical lift, inclined roller conveyors come into play. These systems are essentially roller conveyors that are slanted at an angle, enabling the transport of goods from lower levels to higher ones.
Inclined conveyors are commonly used in areas where there is limited horizontal space, or where vertical movement is necessary, such as in multi-level warehouses. They can handle heavy items like boxes, packages, and pallets, ensuring they reach their intended destination smoothly.
Roller Curves: Navigating Corners with Ease
Most conveyor systems are designed to transport goods in a straight line, but what happens when there’s a need to navigate corners or curves? This is where roller curves come in. By incorporating curves into the conveyor system, businesses can maximize their space, allowing for more efficient routing and product flow.
Roller curves can be used in conjunction with both belt and roller conveyors, providing a seamless transition between straight and curved paths. This not only saves space but also improves the overall efficiency of the conveyor system, reducing delays and potential bottlenecks.
Turntables & Turnouts: Precision in Directional Changes
In some cases, products need to be redirected without disturbing the overall flow of the system. This is where turntables and turnouts prove invaluable.
Turntables: These are devices that rotate items 90 or 180 degrees, allowing products to change direction efficiently. Ideal for sorting applications, turntables can handle items like packages, boxes, and even fragile goods without causing any damage.
Turnouts: While similar to turntables, turnouts allow for a more sophisticated and precise diversion of goods to different conveyor lines or processing areas. These systems are perfect for automated systems that require flexibility in routing.
Chain Conveyors: Heavy-Duty Transport for Tough Applications
For industries that deal with heavy, bulky products or high-temperature environments, chain conveyors are the go-to solution. These systems use a continuous chain to move products along a designated path. The chain provides robust support, making it ideal for handling heavy-duty items like automotive parts, containers, and large boxes.
Unlike roller or belt conveyors, chain conveyors can handle extreme conditions and heavy loads without compromising their structural integrity. Their versatility in handling tough applications makes them indispensable in manufacturing, mining, and other industrial sectors.
Pallet Conveyors: Optimizing Heavy Load Handling
When it comes to transporting large, heavy loads, pallet conveyors are the perfect choice. These systems are designed to move pallets, the primary means of transporting heavy items across industries.
Pallet conveyors can be either powered or gravity-driven, depending on the application. They offer the advantage of securely holding large items in place, reducing the risk of product damage during transit. This makes them ideal for warehousing, assembly lines, and packaging operations.
Pallet Turntables: The Ultimate in Directional Control
In large-scale operations, pallet handling often requires turning products around for easier access or to load/unload goods in different directions. Pallet turntables are the solution to this challenge.
These turntables are designed specifically for palletized goods, allowing pallets to rotate easily, thereby streamlining operations. By integrating turntables into the conveyor system, businesses can significantly improve their product flow, minimize handling time, and increase overall productivity.
The Importance of Conveyor System Integration
Integrating the right conveyor modules is not just about choosing individual components but about ensuring that they work together seamlessly to enhance efficiency. When properly integrated, conveyor systems can create automated workflows that reduce labor costs, improve safety, and boost overall operational speed.
By incorporating various modules such as belt conveyors, roller curves, and chain conveyors, businesses can create customized systems tailored to their specific needs. The result is a smooth, efficient operation that minimizes downtime and maximizes productivity.
Maintenance and Longevity of Conveyor Systems
While conveyor systems are built to be durable, regular maintenance is key to ensuring their longevity. Routine checks on belts, rollers, and chains can prevent unexpected breakdowns, allowing businesses to maintain continuous operations.
Keeping spare parts on hand, along with trained maintenance staff, ensures that minor issues can be quickly resolved before they lead to major disruptions. With proper care, a well-maintained conveyor system can last for many years, providing a solid return on investment.
Conclusion: Investing in the Right Conveyor Solution
Conveyor systems are the unsung heroes of modern-day manufacturing, logistics, and warehousing. Whether you need to move small items across a short distance or transport heavy pallets over long stretches, there’s a conveyor solution tailored to your needs.
By understanding the different types of conveyors and their applications, businesses can make informed decisions that streamline their operations, enhance productivity, and ultimately improve profitability.
As technology continues to evolve, the role of conveyor systems in automation will only grow, leading to even more efficient and cost-effective solutions for industries worldwide.
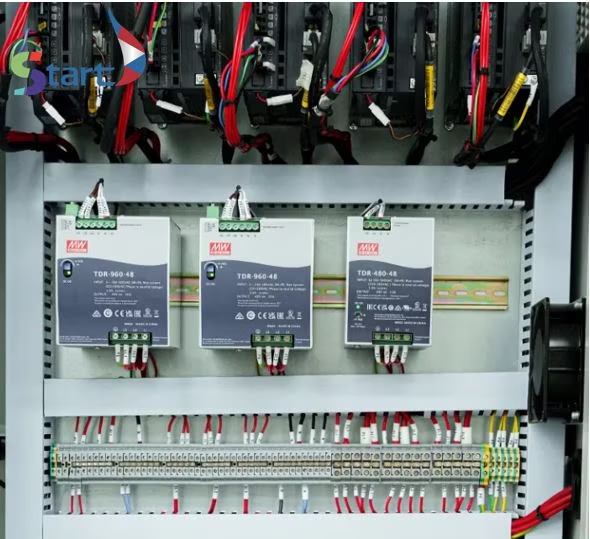
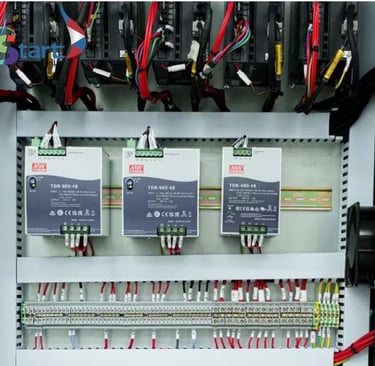