Stitching the Future: Exploring Ultrasonic Sewing Machines and Advanced Sealing Technology
LEON MACHINERY
4/5/20244 min read
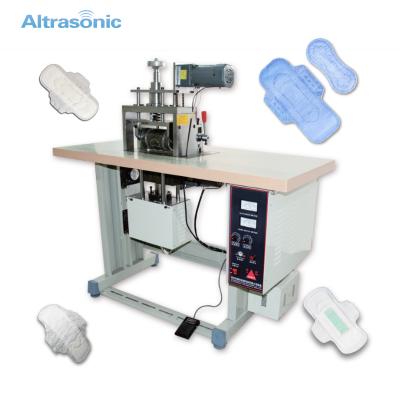
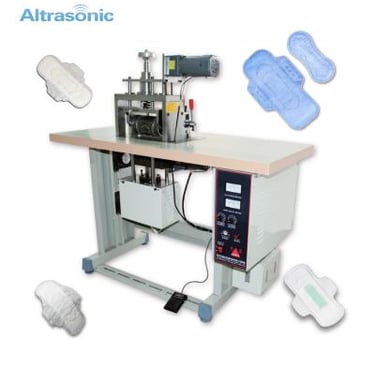
The textile industry has witnessed countless innovations, but none have been as transformative as ultrasonic technology. Ultrasonic sewing machines, combined with cutting-edge sealing and cutting machines, are revolutionizing how fabrics are joined and finished. This blog delves deep into these innovations, uncovering their mechanisms, applications, and the advantages they bring to modern manufacturing.
What is an Ultrasonic Sewing Machine?
An ultrasonic sewing machine uses high-frequency sound waves to bond fabrics together without needles or threads. Instead of traditional stitching, these machines rely on heat generated through ultrasonic vibrations to create durable, seamless bonds.
How It Works
Vibration Generation: The ultrasonic transducer converts electrical energy into high-frequency sound waves.
Material Pressure: Fabrics are pressed together under a horn and anvil system.
Heat Application: Ultrasonic vibrations generate localized heat, fusing the materials.
Continuous Operation: The machine moves the fabric continuously, ensuring smooth and precise seams.
This process is ideal for synthetic fabrics that melt under heat, such as polyester or nylon.
Ultrasonic Lace Sewing Machine: Elegance and Efficiency
The 20kHz lace sewing machine represents a perfect blend of functionality and artistry. Designed for intricate work, this machine creates decorative patterns while ensuring robust seams.
Features of the 20kHz Lace Sewing Machine
Precision Engineering: Capable of producing detailed lace patterns without fraying or distortion.
High Speed: Operates at remarkable speeds, enhancing productivity for mass production.
Versatility: Suitable for applications in fashion, home decor, and industrial textiles.
Applications
Fashion Industry: Crafting delicate lace garments and trims.
Home Furnishings: Creating lace curtains, tablecloths, and pillowcases.
Event Decor: Producing intricate designs for weddings and celebrations.
The combination of speed and detail makes these machines indispensable for industries requiring precision and aesthetics.
Versatile 20kHz and 35kHz Sewing Machines
The choice between 20kHz and 35kHz sewing machines depends on the materials and applications. While the 20kHz machine offers power and durability, the 35kHz version specializes in finer work requiring less energy.
Advantages of 20kHz Machines
High Power Output: Perfect for thick or heavy materials.
Durability: Handles high-volume operations without compromising performance.
Benefits of 35kHz Machines
Delicate Applications: Ideal for lightweight fabrics and intricate designs.
Reduced Noise Levels: Operates more quietly, making it suitable for sensitive work environments.
Common Applications
Automotive Industry: Sewing car seat covers and airbag materials.
Medical Textiles: Creating seamless surgical masks and gowns.
Sportswear: Bonding lightweight, moisture-wicking fabrics.
Ultrasonic Sealing and Cutting Machines: A Game-Changer in Precision Cutting
Ultrasonic sealing and cutting machines offer unparalleled accuracy, ensuring clean edges and strong seals. These machines are especially popular in industries requiring high-quality finishes.
How Ultrasonic Sealing Works
Material Placement: Fabrics or materials are aligned under the ultrasonic horn.
Sealing and Cutting: Vibrations melt the edges, simultaneously sealing and cutting the material.
Edge Reinforcement: Prevents fraying and enhances durability.
This dual-action functionality saves time and ensures consistent results.
The Science Behind Ultrasonic Technology
Understanding the science behind ultrasonic technology is key to appreciating its applications.
The Role of Frequency
The frequency of an ultrasonic machine determines its suitability for different materials:
Low Frequencies (20kHz): Ideal for thicker materials due to higher energy output.
High Frequencies (35kHz and Above): Suitable for delicate or lightweight fabrics.
Energy Efficiency
Ultrasonic machines consume less energy than traditional sewing and sealing methods, contributing to sustainable manufacturing.
Advantages of Ultrasonic Machines Over Traditional Methods
Seamless Bonding: Creates clean, durable seams without threads or adhesives.
High Speed: Enhances productivity, reducing labor costs and time.
Eco-Friendly: Eliminates the need for consumables like glue or thread.
Enhanced Durability: Bonds are often stronger than traditional stitches.
Innovations in Ultrasonic Technology
The field of ultrasonic sewing and sealing is constantly evolving, introducing features that further enhance efficiency and usability.
Automation
Modern ultrasonic machines integrate automation for seamless operation. Features like automatic fabric feeding and tension adjustment ensure consistent results.
Smart Controls
Touchscreen interfaces and programmable settings allow users to customize operations for specific materials and applications.
Compact Designs
Manufacturers are creating compact models suitable for small-scale industries, making ultrasonic technology accessible to a wider audience.
Challenges and Solutions in Ultrasonic Sewing
Challenge: Material Compatibility
Some natural fabrics, such as cotton, may not respond well to ultrasonic welding due to their inability to melt.
Solution: Combine ultrasonic sewing with other bonding techniques or use synthetic blends.
Challenge: Initial Costs
Ultrasonic machines require a significant upfront investment.
Solution: Focus on long-term benefits, such as reduced labor costs and enhanced productivity, to offset the initial expense.
Maintenance Tips for Longevity
Proper maintenance ensures the longevity and performance of ultrasonic sewing and sealing machines.
Regular Cleaning: Remove dust and residue from the horn and anvil.
Alignment Checks: Ensure components are correctly aligned to avoid uneven results.
Component Replacement: Replace worn parts, such as sonotrodes, promptly.
Scheduled Servicing: Conduct periodic maintenance checks with professional technicians.
Choosing the Right Ultrasonic Machine for Your Needs
The wide variety of ultrasonic sewing and sealing machines can make selection challenging. Consider these factors:
Material Type: Synthetic fabrics require lower frequencies, while lightweight materials perform better with higher frequencies.
Application: Identify whether your needs include sewing, sealing, cutting, or all three.
Production Scale: Opt for high-capacity machines for mass production or compact models for small-scale operations.
Support Services: Choose manufacturers that offer training and after-sales support.
The Future of Ultrasonic Sewing and Sealing
The textile industry is heading toward a greener, more efficient future, and ultrasonic technology is leading the charge. As environmental regulations tighten and consumer demand for sustainable products increases, ultrasonic machines provide a viable solution for manufacturers seeking to reduce waste and energy consumption.
Emerging Trends
Biodegradable Materials: Ultrasonic machines are being adapted for use with eco-friendly fabrics.
Customization: Advances in software are enabling highly customized designs and patterns.
Industry Integration: Beyond textiles, ultrasonic sealing and cutting are making their way into packaging and automotive sectors.
Conclusion: Embrace the Ultrasonic Revolution
Ultrasonic sewing machines and sealing technologies are revolutionizing the way fabrics and materials are joined, offering unmatched efficiency, precision, and sustainability. Whether you're crafting delicate lace patterns, sealing medical-grade materials, or cutting durable automotive components, these machines deliver unparalleled performance.
Invest in ultrasonic technology today to elevate your production capabilities and stay ahead in an ever-evolving market. The future of manufacturing is here—and it’s ultrasonic.
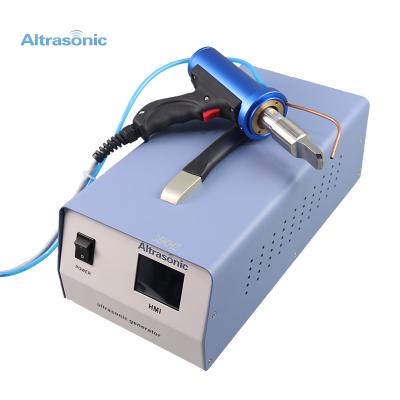
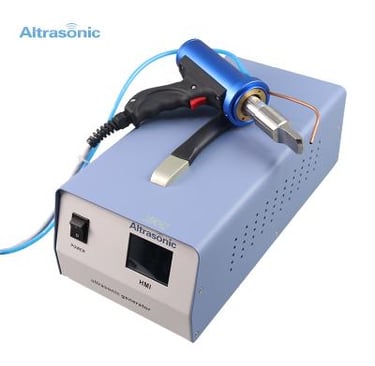