Unlocking the Ultrasonic Frontier: Applications, Devices, and Technology Explained
LEON MACHINERY
12/9/20243 min read
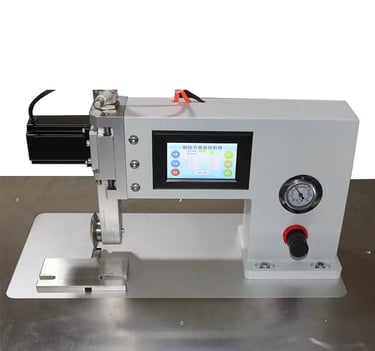
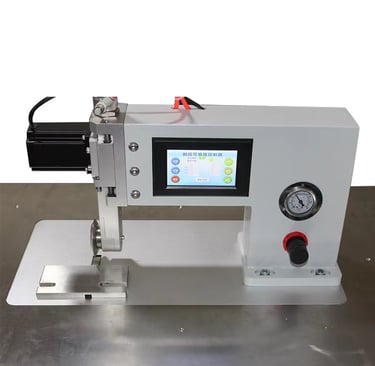
The world of ultrasonic technology is vast and diverse, offering innovative solutions across industries. From welding and machining to cutting and cleaning, ultrasonic devices leverage high-frequency sound waves to perform precision tasks with unmatched efficiency. This blog explores the wide array of ultrasonic devices and their applications, giving you an in-depth understanding of the technology driving them.
What Are Ultrasonic Transducers?
Ultrasonic transducers are at the heart of ultrasonic technology. These devices convert electrical signals into mechanical vibrations using piezoelectric ceramics, which resonate at ultrasonic frequencies. The piezoelectric effect enables precise and high-powered performance across various applications.
For example, a 35 kHz ultrasonic transducer offers excellent heat resistance and is widely used in sewing and cutting machines. Similarly, a 70 kHz transducer is ideal for embedding coil wires into smart cards and RFID cards. Whether for welding, machining, or cleaning, transducers play a critical role in the functionality and reliability of ultrasonic systems.
Categories of Ultrasonic Devices and Their Uses
Ultrasonic Welding Transducers
Ultrasonic welding transducers, such as the 15 kHz and 35 kHz transducers, provide high-quality, steady outputs even under changing loads. These transducers are essential in welding machines, allowing materials like plastics and metals to bond seamlessly.
Ultrasonic Cutting Machines
Ultrasonic cutting machines utilize high-frequency vibrations to achieve precise cuts in materials like plastic, fabric, and even food. A 28 kHz transducer is a popular choice for its high amplitude and reliability in such applications.
Ultrasonic Cleaning Machines
For industries requiring impeccable cleanliness, ultrasonic cleaning machines use transducers like the 25 kHz high-amplitude transducer. These devices ensure effective cleaning of intricate parts in automotive, medical, and manufacturing sectors.
Core Components of Ultrasonic Devices
Piezoelectric Ceramics
The key to an ultrasonic device's efficiency is the piezoelectric ceramic. This material converts electrical energy into mechanical vibrations with high precision. Modern ultrasonic devices often feature multiple ceramic layers for enhanced performance.
Sonotrode
A sonotrode is the tool that delivers ultrasonic vibrations to the target material. Made of titanium or aluminum, it ensures energy transfer with minimal losses.
Booster
The booster amplifies the ultrasonic signal from the transducer, ensuring consistent energy output.
Specialized Ultrasonic Applications
Ultrasonic Plastic and Fabric Cutting
Ultrasonic cutting machines excel in precise, high-speed cutting of delicate materials. They are particularly beneficial in industries like fashion and packaging, where accuracy is crucial.
Ultrasonic Food Cutting
Ultrasonic technology is increasingly being used in the food industry for slicing cakes, bread, and other products without deforming or crumbling them.
Ultrasonic Sewing Machines
Devices like the 35 kHz sewing machine provide seamless stitches in textiles without using threads, offering a sustainable alternative to traditional methods.
Exploring Advanced Ultrasonic Technology
Ultrasonic Homogenizers
Homogenizers are used for mixing and dispersing materials at a microscopic level. They are indispensable in the pharmaceutical, cosmetic, and food industries.
Ultrasonic Machining
Machining applications, such as drilling and milling, benefit from the precision and efficiency of ultrasonic vibrations. These devices excel in shaping hard materials like ceramics and glass.
Replacing and Upgrading Ultrasonic Devices
As technology evolves, so do ultrasonic devices. Replacement converters like the Herrmann 35 kHz ultrasonic converter ensure compatibility and high performance in modern machines. Brands such as Branson, Dukane, and Telsonic offer replacement transducers tailored to specific industrial needs.
Why Choose High-Quality Ultrasonic Devices?
Investing in high-quality ultrasonic devices ensures longevity, efficiency, and reduced maintenance costs. Devices with heat resistance, such as the 40 kHz transducer, perform well in challenging environments and contribute to overall operational reliability.
Key Considerations for Selecting Ultrasonic Equipment
Frequency: The device's frequency determines its suitability for specific applications. For example, 70 kHz transducers are ideal for micro-scale welding, while 15 kHz transducers are better suited for larger tasks.
Power: Higher power ratings, like 2600W ultrasonic transducers, handle demanding applications with ease.
Material Compatibility: Ensure the device is compatible with the materials you intend to work on.
Ultrasonic Devices in Action: Real-World Applications
Automotive Industry: Ultrasonic technology aids in welding plastic components and cleaning engine parts.
Medical Field: From surgical tools to cleaning devices, ultrasonic equipment ensures precision and hygiene.
Textile Industry: Ultrasonic sewing machines enhance production efficiency while reducing waste.
Maintaining and Upgrading Ultrasonic Equipment
Regular maintenance and timely upgrades are crucial for optimal performance. Modern impedance analyzers and other measuring equipment help monitor device efficiency and identify potential issues.
Conclusion
Ultrasonic technology has revolutionized countless industries, offering sustainable and efficient solutions for complex tasks. Whether you’re looking for a high-frequency ultrasonic transducer or a specialized ultrasonic cutting machine, understanding the intricacies of these devices can help you make informed decisions. Embrace the ultrasonic frontier and elevate your operations with cutting-edge technology.
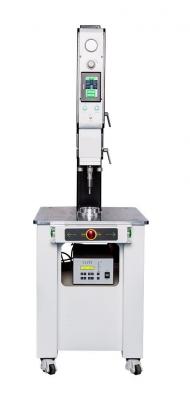
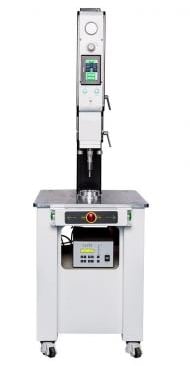