The Silent Revolution: Unveiling Ultrasonic Welding Machines and Their Applications
LEON MACHINERY
6/7/20244 min read
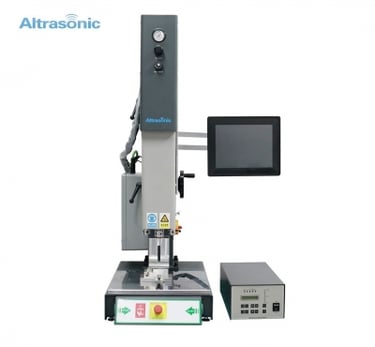
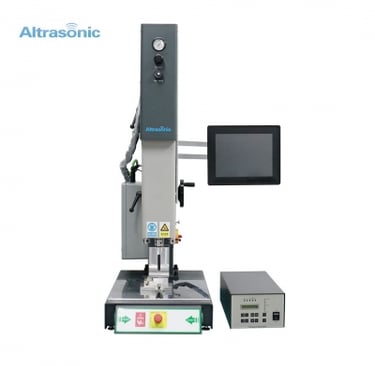
Ultrasonic welding machines are transforming industries by offering a seamless, efficient, and environmentally friendly way to bond materials. From plastics to metals, these machines cater to a variety of applications, ensuring high precision and superior performance without the need for adhesives, fasteners, or excessive heat. In this comprehensive guide, we’ll explore the types of ultrasonic welding machines and their game-changing applications across industries.
What is Ultrasonic Welding?
Ultrasonic welding is a process that uses high-frequency sound waves to join materials together. This method is particularly effective for plastics and metals, where traditional bonding techniques might fall short.
Here’s how it works:
Vibration Generation: Ultrasonic welding machines produce vibrations in the range of 15kHz to 70kHz.
Pressure Application: These vibrations are directed at the materials to be joined while applying moderate pressure.
Heat Generation: The friction caused by the ultrasonic waves generates localized heat, which melts the materials at the interface.
Bond Formation: As the materials cool, they solidify into a robust and durable joint.
The result is a seamless bond that requires no consumables and generates minimal waste.
Ultrasonic Plastic Welding Machines: Versatility and Precision
Ultrasonic plastic welding machines are widely used for bonding thermoplastics. These machines excel in creating strong, clean, and fast welds without damaging the surrounding materials.
Key Features
High Efficiency: Welds are completed in fractions of a second.
Non-Destructive Process: Ultrasonic welding does not compromise the structural integrity of the materials.
Environmentally Friendly: No adhesives, solvents, or emissions are involved.
Applications
Automotive Industry: Welding dashboards, light fixtures, and interior components.
Consumer Electronics: Bonding casings for smartphones, laptops, and other gadgets.
Medical Devices: Manufacturing disposable syringes, catheters, and filtration systems.
Ultrasonic Spot Welding Machines: The Power of Precision
Spot welding involves joining materials at specific points rather than along a continuous seam. Ultrasonic spot welding machines are highly effective for applications requiring precise and localized bonding.
Advantages
Minimal Heat Impact: The process generates localized heat, preventing warping or damage.
Rapid Operation: Spot welds can be completed in milliseconds.
Cost-Effective: Reduces material usage and eliminates the need for consumables.
Common Uses
Textile Industry: Welding synthetic fabrics for garments and industrial applications.
Packaging: Sealing blister packs, food containers, and cosmetic packaging.
Small-Scale Repairs: Fixing minor defects in plastic or metal components.
Ultrasonic spot welding is especially favored in industries where precision and speed are critical.
Ultrasonic Metal Welding Machines: Redefining Strength
While ultrasonic welding is often associated with plastics, it has significant applications in metal bonding. Ultrasonic metal welding machines use vibrations to create strong, electrical, and thermal connections between metal surfaces.
Key Attributes
Non-Fusion Welding: Bonds metals without melting them, preserving their properties.
High Conductivity: Ideal for electrical connections in wiring and circuitry.
Durable Joints: Produces welds that withstand mechanical and thermal stresses.
Industry Applications
Automotive: Welding battery terminals and electrical connectors.
Aerospace: Creating lightweight yet strong components for aircraft.
Energy Sector: Bonding components in solar panels and wind turbines.
How Ultrasonic Welding Machines Work
Components of an Ultrasonic Welding Machine
Generator: Converts electrical energy into high-frequency signals.
Converter: Transforms these signals into mechanical vibrations.
Booster: Amplifies the vibrations for enhanced energy transfer.
Sonotrode: Directs the vibrations to the welding surface.
Fixture: Holds the materials in place during the welding process.
The Welding Process in Detail
Setup: Materials are positioned in the fixture.
Energy Transmission: The sonotrode delivers ultrasonic waves to the materials.
Material Fusion: Friction-generated heat melts the materials at the contact points.
Cooling and Bonding: The melted interface solidifies, forming a robust joint.
This precise process minimizes material waste and energy consumption, making it both cost-effective and environmentally friendly.
Innovations in Ultrasonic Welding Technology
The ultrasonic welding industry is continuously evolving, driven by advancements in technology. Recent innovations include:
Smart Ultrasonic Machines
Modern machines come equipped with sensors and software that provide real-time feedback on weld quality, energy usage, and machine performance. This ensures consistent results and reduces the risk of errors.
Modular Systems
Manufacturers are designing modular machines that allow for quick changes in components such as sonotrodes and boosters. This flexibility is particularly beneficial in industries with diverse product lines.
Eco-Friendly Applications
Ultrasonic welding is being integrated into green manufacturing processes, such as recycling plastics and reducing waste in packaging.
Benefits of Ultrasonic Welding Machines
Speed: Welding cycles are completed in milliseconds, enhancing production efficiency.
Cleanliness: The process is free of fumes, debris, or chemical residues.
Safety: No open flames or hazardous materials are involved.
Versatility: Applicable to a wide range of materials and industries.
Challenges and Solutions
While ultrasonic welding offers numerous advantages, it also comes with challenges:
Challenge: Material Compatibility
Not all materials are suitable for ultrasonic welding. For example, certain plastics may not generate sufficient friction for bonding.
Solution: Conduct material compatibility tests and opt for hybrid solutions if needed.
Challenge: Equipment Costs
High-quality ultrasonic welding machines can be expensive.
Solution: Consider long-term benefits such as reduced operational costs and higher productivity to justify the investment.
Maintenance Tips for Ultrasonic Welding Machines
To ensure the longevity and performance of your welding machine, follow these maintenance tips:
Regular Cleaning: Remove any residue from the sonotrode and fixture.
Alignment Checks: Ensure the machine components are properly aligned to avoid uneven welds.
Calibration: Periodically calibrate the machine to maintain precision.
Spare Parts: Keep essential components like boosters and converters readily available.
Choosing the Right Ultrasonic Welding Machine
Selecting the right machine depends on several factors:
Material Type: Determine whether you’re working with plastics, metals, or composites.
Application Requirements: Identify the specific tasks, such as spot welding or continuous welding.
Frequency and Power: Match the machine's frequency and power output to your application needs.
Support and Training: Opt for manufacturers that provide comprehensive training and after-sales support.
Investing in the right ultrasonic welding machine can significantly enhance your operational capabilities.
Conclusion: The Future of Ultrasonic Welding
Ultrasonic welding machines represent the future of efficient and sustainable manufacturing. Whether you’re bonding plastics, metals, or composites, these machines offer unparalleled speed, precision, and versatility. By understanding the types of ultrasonic welding machines and their applications, businesses can make informed decisions that drive innovation and productivity.
As industries continue to evolve, the role of ultrasonic welding will only grow. Embrace this silent revolution and position your business at the forefront of technological advancement.
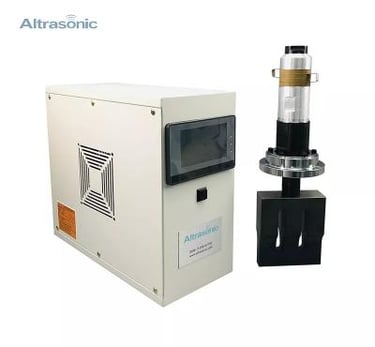
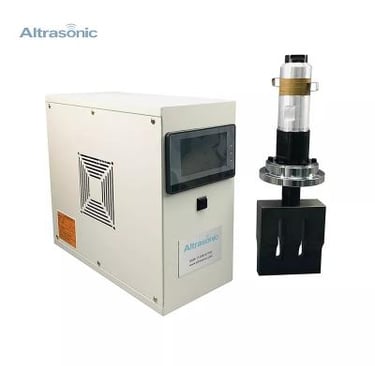