Unlocking Ultrasonic Potential: A Guide to Ultrasonic Transducers and Their Applications
LEON MACHINERY
8/9/20243 min read
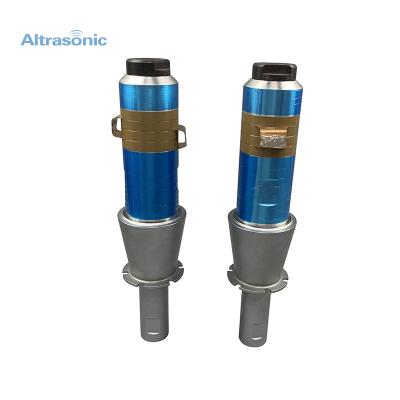
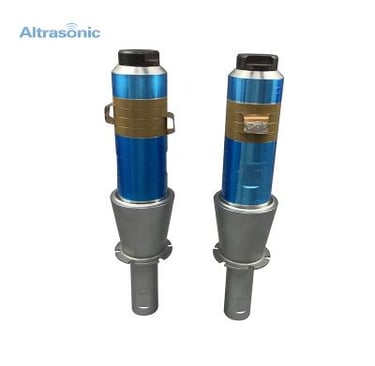
Ultrasonic technology has revolutionized industries by delivering precision and efficiency through high-frequency vibrations. Ultrasonic transducers, the heart of this technology, come in a wide range of frequencies to suit diverse applications. Whether for welding, cutting, or cleaning, understanding the nuances of ultrasonic transducers can unlock new possibilities for your business.
What is an Ultrasonic Transducer?
At its core, an ultrasonic transducer is a device that converts electrical energy into high-frequency mechanical vibrations. This transformation occurs through the piezoelectric effect, where piezoelectric ceramics resonate to create ultrasonic waves. These waves are then harnessed for various industrial and commercial purposes, ranging from welding to machining and beyond.
The versatility of ultrasonic transducers lies in their frequency ranges, which cater to specific applications:
15kHz Ultrasonic Transducer: Used in heavy-duty welding and cutting applications.
20kHz Ultrasonic Transducer: Balances power and precision, ideal for plastic welding.
25kHz Ultrasonic Transducer: Excels in high-power industrial cleaning.
28kHz Ultrasonic Transducer: Favored for precise cutting applications.
30kHz Ultrasonic Transducer: Offers specialized solutions for lightweight materials.
35kHz Ultrasonic Transducer: A popular choice for delicate tasks like sewing and sealing.
40kHz Ultrasonic Transducer: Ideal for detailed cleaning and small-scale applications.
50kHz Ultrasonic Transducer: Suitable for micro-machining and intricate tasks.
55kHz Ultrasonic Transducer: Used in advanced medical and scientific equipment.
60kHz Ultrasonic Transducer: Provides ultra-precise control for high-tech applications.
70kHz Ultrasonic Transducer: Designed for embedding and micro-welding tasks.
Ultrasonic Welding Transducers: Precision Meets Strength
One of the most transformative uses of ultrasonic transducers is in welding. Ultrasonic welding transducers operate at various frequencies to bond materials without the need for adhesives, fasteners, or heat.
15kHz Ultrasonic Welding Transducer: These transducers deliver high energy, making them suitable for welding thick or rigid plastics. Their robustness ensures reliable performance in industrial environments.
35kHz Ultrasonic Welding Transducer: Offering a balance of power and delicacy, these transducers are perfect for smaller, more intricate welding tasks, such as medical device assembly or electronics.
With the right welding transducer, businesses can achieve stronger bonds, faster production cycles, and reduced operational costs.
The Role of Frequency in Ultrasonic Transducers
Frequency is a critical parameter in ultrasonic applications. Lower frequencies, such as 15kHz and 20kHz, produce greater amplitude, making them ideal for demanding tasks like welding and heavy-duty cutting. Higher frequencies, like 50kHz and 70kHz, deliver precision and are often used in micro-machining and sensitive applications.
Key Advantages of Frequency-Specific Applications
15kHz Ultrasonic Transducer: High amplitude ensures effective welding of dense materials.
28kHz Ultrasonic Transducer: Precision cutting of fabrics and plastics.
70kHz Ultrasonic Transducer: Ultra-precise micro-welding for advanced manufacturing.
Selecting the right frequency optimizes performance, minimizes energy consumption, and enhances durability.
Applications Across Industries
Automotive Industry
Ultrasonic transducers are indispensable in the automotive sector for assembling components, cleaning intricate parts, and cutting specialized materials. 20kHz transducers are commonly used to weld dashboards, while 25kHz transducers excel in cleaning fuel injectors.
Medical and Scientific Equipment
The high precision of 55kHz and 60kHz ultrasonic transducers makes them ideal for producing medical devices and laboratory tools. Their ability to operate without introducing contaminants is critical in these fields.
Textile and Packaging Industries
Ultrasonic sewing and sealing machines, powered by 30kHz and 35kHz transducers, are transforming the textile industry. These devices offer threadless stitching, reducing waste and enhancing production efficiency.
Advancements in Ultrasonic Technology
The ultrasonic field is continually evolving, introducing new technologies and capabilities:
Smart Ultrasonic Transducers: With embedded sensors and real-time monitoring, these devices adapt to changing conditions for consistent output.
Modular Systems: Swappable components like boosters and sonotrodes allow for customization and flexibility.
Eco-Friendly Applications: Ultrasonic transducers are being employed in green initiatives, such as energy-efficient cleaning systems.
Maintaining and Upgrading Ultrasonic Systems
To maximize the lifespan and efficiency of ultrasonic devices, regular maintenance is essential. Key practices include:
Inspecting and replacing piezoelectric ceramics periodically.
Monitoring impedance levels using advanced measuring equipment.
Upgrading components like the 35kHz ultrasonic welding transducer to enhance performance.
Ultrasonic Innovations: What’s Next?
The future of ultrasonic technology is poised to bring further advancements in:
Nano-Manufacturing: Using high-frequency transducers for atomic-scale precision.
Sustainable Solutions: Incorporating ultrasonics in renewable energy applications.
Smart Manufacturing: Integrating AI with ultrasonic systems for predictive maintenance and adaptive performance.
Choosing the Right Ultrasonic Transducer
When selecting an ultrasonic transducer, consider the following factors:
Application: Match the transducer's frequency and power to your task.
Durability: Heat resistance and build quality are crucial for long-term use.
Support: Opt for devices with reliable after-sales service and easy access to replacement parts.
Investing in high-quality transducers ensures consistent results and lowers overall operational costs.
Final Thoughts: Harnessing Ultrasonic Power
Ultrasonic technology offers a world of possibilities, from welding and cutting to cleaning and sealing. By understanding the nuances of ultrasonic transducers and their frequency-specific applications, businesses can unlock unparalleled efficiency and precision.
Embrace the potential of ultrasonic technology to drive innovation in your industry. Whether it's a 15kHz welding transducer for heavy-duty tasks or a 70kHz transducer for micro-precision applications, the right ultrasonic device can redefine your operational capabilities.
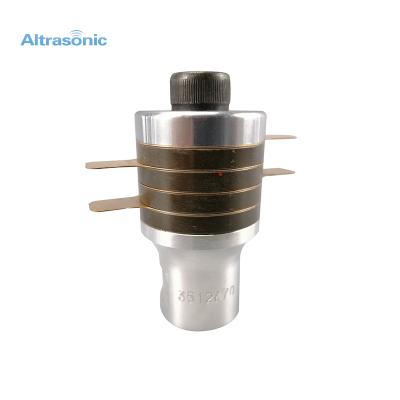
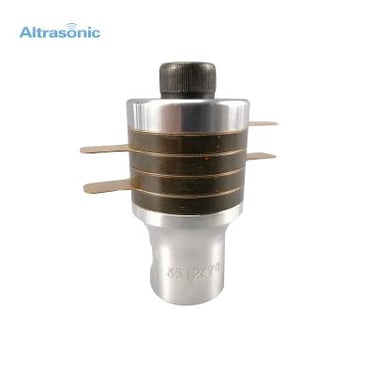